電動閥門智能控制器的設計
以AT80C2051作為微控制器設計電動閥門智能控制器,完成了電動閥門的位置檢測、遠程控制信號轉換、參數整定與靈敏度調整、閥門電機驅動電路及鍵盤、顯示等硬件電路設計,在建立數學模型的基礎上,設計并驗證了系統的PID算法,完成了電路中相應的軟件程序設計,實現了對電動閥門執行機構進行實時控制,保證了操作的可靠性與精確性。運用RS-485實現與遠程控制中心間的通訊,在組態環境下進行實時監控運行,實現儀表控制的數字化、智能化、網絡化與遠程化,便利了操作,拓寬了閥門的使用環境范圍,節約了成本。組態實驗調試的結果表明:該裝置線性關系較好,動作時間短,具有較高的精度與友好的人機界面,誤差在0.3%以內。
在現代工業自動控制中,調節閥是最主要的執行器件之一,在石油、化工、電力、水利等行業發揮著重要的作用。但國內電動調節閥技術與國外相比還有很大差距,國內電動調節閥普遍具有結構不合理,控制精度低,安全性能差,不能很好地進行人機通話、難于現場標定和維修等缺陷。隨著電子技術、控制技術及通訊技術的發展,國內閥門廠家紛紛對電動調節閥進行研究,各項指標和性能都有所提高,但是相應的成本也提高不少,價格比較昂貴的。為此研究一款價格實惠、結構簡單、功能齊全、便于現場操作和集中控制的電動調節閥。
1、硬件結構
1.1、總體結構
系統的硬件電路主要由閥門的位置反饋信號檢測、遠端控制信號的轉換和現場參數整定與靈敏度調整電路所構成的模擬量輸入通道、A/D轉換、伺服電機驅動及減速運行的輸出電路、D/A轉換和外圍鍵盤顯示等電路以及上位機遠程通訊等組成,如圖1所示。控制中心信號、現場實際開度的反饋信號、現場參數整定和靈敏度信號調整通過TL2543進行A/D轉換后送到AT89C2051微控制器,微控制器根據這些信號進行運算處理,以控制電動閥門執行機構的正反運轉和全開全關運行,使得閥門快速達到設定開度。采用LCD實時顯示閥門實際開度值,通過RS-485通訊直接將閥門現場反饋信號傳輸到監控中心的上位機,在上位機的組態界面上進行顯示,以記錄閥門開度的調節情況。同時中控中心的工作人員可以通過組態監控,對現場閥門實際開度進行設定,信號通過RS-485直接送回給控制器進行操作。在電動閥門出現故障時,現場可以及時地做出報警,同時控制中心組態監控也會發出報警,以采取相應的保護措施。通過D/A將閥的開度轉換為4~20mA的電流信號,傳輸給遠程控制中心的模擬量采集模塊,以進行遠程操作與顯示。
1.2、輸入通道電路設計
輸入通道主要由閥門位置檢測信號、遠端控制中心信號、現場參數整定與靈敏度調整電路與A/D轉換電路組成。
用安裝在閥門電動機執行機構上的位置變送器來檢測實際開度反饋信號,位置變送器是高性能的導電塑料精密旋轉電位器,具有較高分辨力的、高性能的經濟類型產品。電位器旋轉角度和閥門開度有線性關系,旋轉電位器將閥門開度情況轉換成對應的角度信號,進而轉換成系統所接收1~5V的DC電壓信號,因此可以依據電壓和角度的線性關系得到相應的位置信號。閥門實際開度反饋信號閥門實際開度經過位置檢測機構轉換成相應的電壓信號MA2,經過射級跟隨器進行阻抗處理變化之后的信號送到A/D轉換芯片TL2543的IN1口。電路如圖2所示,其中VD3、VD45起到鉗位作用。
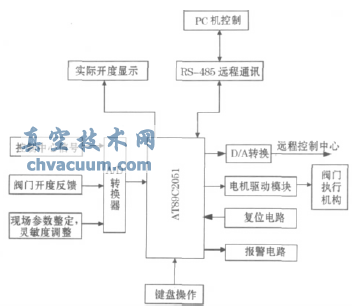
圖1 系統結構圖
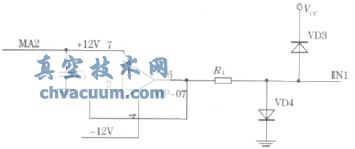
圖2 控制端信號轉換電路圖
工業生產中傳送的標準的電信號可能是4~20mA的直流電流,也可能是1~5V的直流電壓,控制中心的信號為4~20mA的電流信號,當來自控制中心的信號MA1經過圖3所示的信號轉換電路時,預先應當將MK2閉合,此時電流輸入信號經電阻R2、GND形成回路,4~20mA的電流信號經過轉換電阻R2流向地,此時的輸入電流信號就被轉換成1~5V的電壓信號,即A/D轉化器TL2543的IN0口的電位。亦即信號的最小值4mA或1V對應精密電位器的最小值,也相當于閥門的起點位置。信號最大值20mA或5V對應精密電位器的最大值,也相當于閥門滿度位置。
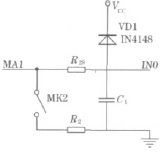
圖3 位置采集信號轉化電路
為使閥門執行器能夠適應工業生產中不同型號與口徑閥門,滿足各種的閥門裝置具有不同的初始位置和滿度位置,提高系統的靈敏度,增強通用性,做到測量的精確性,采用3個滑動電阻RP1、RP2、RP3構成調零、調滿和調靈敏度電路,使閥門電動執行機構的零點和最大角位移都在一定范圍內可調,減小誤差。調零(ZERO)、調滿(SPAN)、靈敏度(PROP)電路如圖4所示。IN2、IN3、IN4端的電壓就為傳輸到A/D轉換TL2543的調滿、調零和靈敏度信號。閥門在運行之前要將這些信號進行A/D轉換反饋到為微控制器中進行處理,來控制電動執行機構下一步的轉向。
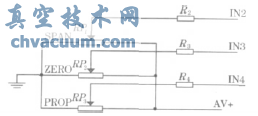
圖4 零點、滿量程、靈敏度調整電路
1.3、閥門電機驅動電路設計
微控制器將轉換之后的控制信號、閥門實際開度反饋信號、靈敏度信號等進行相應的運算,判斷閥門執行機構該向哪個方向運行,從而向對應的I/O口送出相應的TTL觸發信號,信號經過2個或門互鎖正反轉觸發和轉換電路與固態繼電器的觸發控制電路轉換成可以驅動伺服電機運動的交流控制電平,圖5中單片機控制器發出2個TTL觸發信號,運用與非門的功能,將電機的正轉、反轉、停用工作狀態用P3.2、P3.3電平狀態來控制,P3.2、P3.3的TTL觸發信號經過與非門傳輸到固態繼電器38D05的DC-上,為防止兩個觸發器信號同時為低電平導通,在固態繼電器的DC+處分別接上拉電阻,已在初始化的時候把觸發信號拉成高電平,避免誤導通,從而達到閥門的正反、停止控制。同時電路中接入極限位置行程開關,當閥門運轉至極限位置,電機停止運轉,起到保護的作用。為了準確及時平穩控制閥門的位置,在伺服電機驅動增加減速器,減速器采用諧波齒輪傳動,把伺服電機高速轉矩、小力矩的輸出功率轉換成執行機構輸出軸的低轉速、大力矩的輸出功率,以推動調節結構,使閥門運行平緩、承載能力強、傳動精度高。
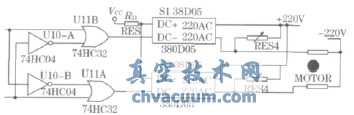
圖5 閥門電機驅動電路
2、系統控制算法與仿真
2.1、系統建模
閥門控制屬于典型的位置隨動控制系統,由位置檢測機構檢測到的信號與實際信號相比較產生誤差信號,經過控制器進行A/D轉換后進行PID運算,參數調整等輸出電壓與測速發電機反饋電壓形成的誤差電壓作為伺服電機驅動電壓,通過減速器后輸出實際角度。控制系統結構框圖如圖6所示。
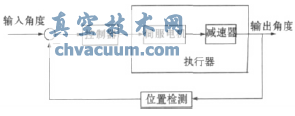
圖6 閥門控制系統結構圖
伺服電機部分的傳遞函數可以表示為:

式中:電機增益kt=2;Ra=6Ω;La=12mH;轉動慣量J=0.006kg·m2;Ce=Cm=0.3N·m/A;黏性摩擦系數f=0.2N·m/s;減速比i=0.1。減速器部分可以看出以純積分環節。
2.2、PID控制與仿真
采用PID控制算法,通過臨界比例度法與湊試法整定PID控制器的參數,得到Kp=10,Ti=0.01,Td=0.5,其正弦輸入下跟隨曲線如圖7所示。
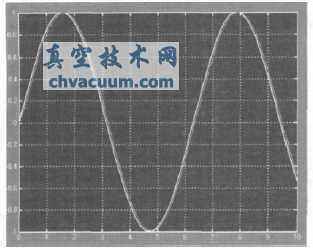
圖7 電動閥門跟隨曲線
從圖7可以看出輸入輸出曲線基本一致,跟隨特性好,調節速度快,能夠滿足設計要求。
3、系統軟件設計
開機初始化,由上電復位后的主程序執行,用來初始化系統的硬件資源和軟件資源,對串行口、定時器、內部寄存器初始化;完成開機電信號故障檢測,如果有電信號故障則亮紅燈報警,沒有故障則進行鍵盤掃描,判斷是否有強制執行設置,有則執行相應動作,沒有則采集檢測的位置信號,與設定值和控制中心命令值比較,以調整參數,開啟A/D轉換并數字濾波,經過PID運算后,驅動閥門動作,控制電機轉動的方向與角度,并顯示相應閥門實際開度。同時向上位機實時提供實際開度數據信息,顯示閥門開度,故障報警等。
4、試驗調試
遠程監控中心PC采用組態進行程序設計,通過PC的串行接口傳輸和接收數據,在該界面中預設閥門的開度以及實時開度顯示,歷史數據報表的查閱。
表1為從組態界面上讀取的電動閥預設開度和實際開度之間的實時數據。
從表1中可以看出閥門實際開度值與預設開度值基本一致,最大誤差僅0.25%,符合設計要求達到的精度。
組態運行下閥門開度值K與相應出口流量Q間測得的數據報表如表2所示。
表1 預設開度與實際開度對比
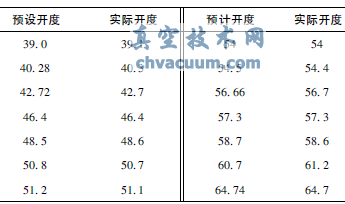
表2 系統歷史數據報表
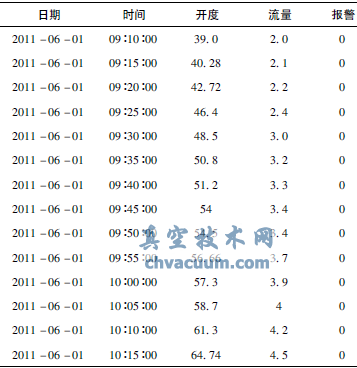
對以上數據利用MATLAB進行多項式擬合,擬合曲線如圖8所示。
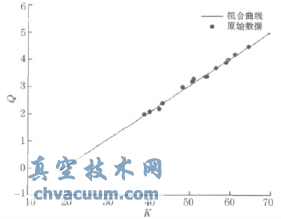
圖8 閥門輸出曲線
從圖8中可以看出出口流量和閥門開度成正比的線性關系,其關系式為:Q=0.0983K-1.8621,線性關系理想。
由圖表分析可知,在相同變化行程情況下,閥門開度較小時,相對流量變化值小,比較緩和;閥門開度較大時,控制靈敏有效。所以在實際中用控制閥門開度來控制流量大小。
5、結束語
以單片微機為控制器設計了電動閥門控制器,能夠接收控制中心命令信號和鍵盤控制命令,根據閥門實際反饋信號實現正轉、反轉、停轉的閉環控制;能夠根據實際運行狀況做出判斷,進行故障報告、應急處理、顯示等工作;具備遠程通信功能,能夠在組態環境下進行監控運行,實現儀表控制的數字化,智能化、網絡化與遠程化,拓寬了電動閥門的使用環境的范圍,節約了成本。實驗調試的結果表明:該裝置線性關系較好,動作時間斷,誤差在0.3%以內,具有較高的精度。