旋塞閥閥體的變形分析與結構優化
為了解決旋塞閥閥體密封泄漏問題,采用在閥體外側布置加強圈、加強筋的方法以降低閥體應力和變形。利用有限元模擬對比分析,并采用復合形法優化加強圈、加強筋結構。結果表明,優化后,閥體密封良好,閥體體積增加最小。
旋塞閥是最早被人們用來截流的設備,其應用廣泛。目前,許多研究者對閥體變形及結構優化做了大量工作,但只是單純的軟件模擬計算。旋塞閥閥體是三通結構,把中腔看做主管,流道視為支管。由于閥體開孔處產生很高的應力集中,使密封面產生較大變形而導致密封泄漏。因此,為了降低應力集中和過大變形,可在開孔附近補強。以下通過在旋塞閥外壁布置加強圈、加強筋結構,并采用復合形法優化,以保證閥門的安全性和經濟性。
1、數學模型
1.1、設計變量
在閥體流道開孔壁面上下各設置n道橫向加強圈,在橫向加強圈之間設置m道縱向加強筋。將所有加強圈、加強筋壁厚都設定為閥體壁厚。在開孔附近進行補強,故取n=1,m=4,則設計變量為4,上、下橫向加強圈的寬度分別為h1、h2,縱向加強筋跨度β、高度H,如圖1(a)、(b)所示.設計變量為X=[x1x2x3x4]T=[h1h2βH]T。
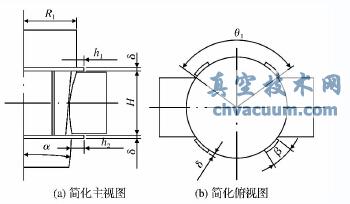
圖1 閥體加強圈及加強筋結構
1.2、性能約束
(1)閥體強度
加強圈在其間距段的全面積上均勻地承受內壓,將橫向和縱向加強筋的壁厚等效均勻地分布到閥體上,取橫向加強圈與縱向加強筋對閥體增加的當量壁厚的平均值為Δδ(X),則

其中:δ為閥體壁厚(mm);θ1為閥體實際角度的一半(°)。三通結構閥體是薄壁管件,在內壓作用下,除承受薄膜應力外(受到應力集中系數的影響),還存在彎曲應力的作用。主管可看成受內壓p及支管與閥體相貫線上受拉力q的共同作用。內壓p產生的環向應力為
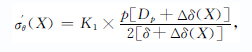
內壓P產生的軸向應力為
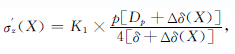
其中:Dp為主管平均直徑(mm);K1為應力集中系數。支管的單位長度拉力為
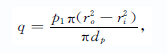
其中:dp為支管平均直徑(mm);p1為密封比壓(MPa);ro、ri分別為閥體密封面的外半徑、內半徑(mm)。
q可分解成主管徑向力q′=qcosα1及環向力q″=qsinα1。它們所產生的環向及軸向應力可近似為
δ0為支管壁厚(與閥體壁厚δ相等)(mm);α1為q′與支管軸線的夾角(°);μ為泊松比。根據圓筒容器小開孔應力分析,開孔最大應力發生在α1=0處,將該值代入式(5)、式(6),可得環向應力
根據最大剪應力強度理論:對于薄壁元件,徑向應力為σ3(X)=σr(X)=0。比較式(7)、式(8)中,σθ(X)、σz(X)的大小,σθ(X)=σ1(X)。則當量應力為σd(X)=σ1(X)-σ3(X)≤[σ]。
(2)密封面變形
根據物理方程和幾何方程,通過積分求得密封面處閥體變形如下:
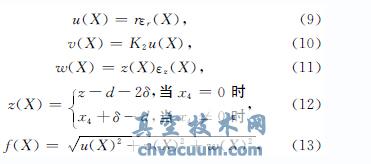
其中:d為支管內徑(mm);z為閥體高度(mm);r為閥體中徑處半徑(mm);K2為閥體除開孔處弧度;
εr(X)、εz(X)分別為徑向應變、軸向應變;u(X)、υ(X)、w(X)、z(X)、f(X)分別為閥體徑向變形、周向變形、軸向變形、閥體等效高度及總體變形(mm)。
1.3、目標函數及邊界約束
(1)目標函數
加強圈和加強筋的體積若為ΔV(X)。要使ΔV(X)最小,必須滿足性能約束的臨界條件:①滿足應力要求:σd=σ1-σ3=[σ]時,得到閥體增加當量壁厚δ1;②滿足變形要求:f(X)=0.001DN時,閥體變形滿足密封要求,得到閥體增加當量壁厚δ2,其中DN為閥體公稱直徑。則取Δδ(X)=max(δ1,δ2),其最小體積為

其中:θ2為閥體周角(°);r1為支管外半徑(mm);R1為錐形閥體大端外半徑(mm)。
(2)邊界約束
條件為ximin≤xi≤ximax(i=1,2,3,4),其中:ximax、ximin分別為設計變量上、下極限。
2、實例分析
以材料為ZG1Cr5Mo,公稱直徑為DN=200mm的旋塞閥為例,其物理參數及結構參數見表1。
表1 物理參數及結構參數
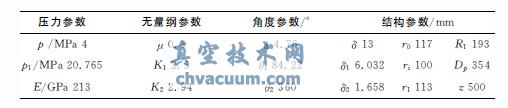
2.1、原設計結構閥體應力及變形分析
根據閥體物理參數及結構參數,由理論計算公式(7)、式(13)和數值計算方法分別計算閥門關閉時原設計結構閥體應力和變形,計算結果如表2所列。數值計算云圖如圖2、圖3所示。
表2 原設計結構閥體應力及密封面變形分析
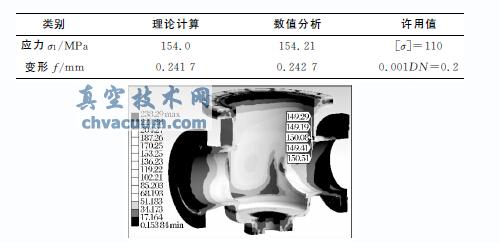
圖2 原設計結構閥體強度
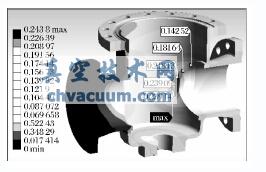
圖3 原設計結構密封面變形
由上述計算結果可知:閥體開孔處的應力大于許用應力,主管與支管交界處變形量>0.001DN,該閥體應力及密封面變形都不滿足要求.綜上所述,該閥體需要設置加強件以降低應力集中及密封面變形,我們采用復合形法優化設置加強圈和加強筋。
2.2、加強圈、加強筋結構參數優化
加強圈、加強筋設計變量極限值如表3所列。取復合形頂點數P=5,反射系數γ=1.3,精度
各設計變量對目標函數的影響分別見圖4(a)、(b)、(c)、(d)。
各設計變量共同作用下,ΔV(X)變化大致有以下規律:上、下橫向加強圈寬度越小,體積越小,當分別趨于13mm、14mm時,體積最小;縱向加強筋跨度越大,體積越小,當趨于36.8°時,體積最小;縱向加強筋高度越小,體積越小,當趨于234mm時,體積最小。
2.3、優化結構閥體應力及變形分析
利用體積最小的設計變量優化閥體加強圈和加強筋結構,通過理論計算及有限元數值模擬分析閥體開孔處的應力σ1(X*)和密封面變形f(X*),計算結果見表4。優化后,閥體應力云圖見圖5,密封面變形云圖見圖6。
由表4可以看出,兩者計算結果基本吻合,閥體應力約等于應力臨界值,閥體密封面變形滿足變形條件。
3、結論
(1)三通結構旋塞閥開孔處產生的應力集中,使閥體密封面變形過大而導致密封泄漏。為解決上述問題,在閥體外側布置加強圈及加強筋結構,并采用復合形法優化。
(2)最優化結果表明:適當減小橫向加強圈寬度,增大縱向加強筋跨度,降低縱向加強筋高度,會使加強圈和加強筋的體積減小,優化后比優化前體積降低了20.96%。
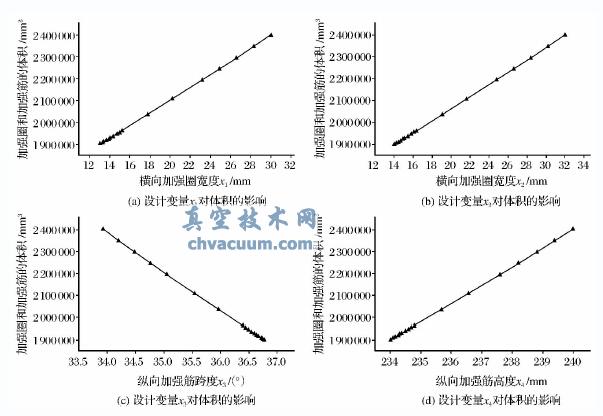
圖4 各設計變量對目標函數的影響
表4 優化結構閥體應力及密封面變形分析
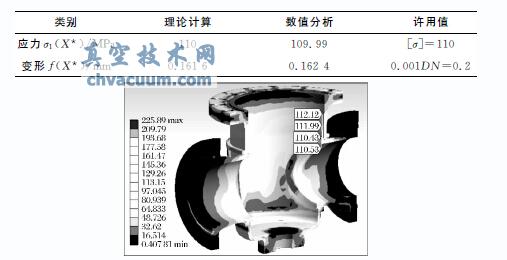
圖5 優化結構閥體強度
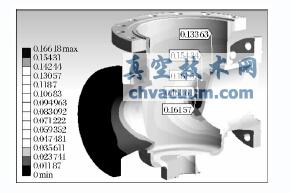
圖6 優化結構密封面變形
(3)優化后的閥體應力及密封面變形分別滿足各自的規定要求,比原設計結構的閥體應力和密封面變形量分別降低了28.57%和33.14%。