液氨充裝球閥泄漏原因分析及處理對策
1、現狀和存在的問題
云南天安化工有限公司生產的合成氨主要以管道輸送和汽車充裝運輸供給用戶。汽車充裝設計年充氨能力12萬噸,由三組充裝臺組成。充氨壓力1.58~1.60MPa,溫度約-40℃。
液氨充裝站大量采用Q47F-25P,DN50mm型球閥,使用過程中頻繁發生泄漏,后又改為同類型低溫球閥,即DQ47F-25P,DN50mm型(耐溫約-46℃),仍然發生泄漏,多次被迫進行置換檢修。置換時間約3h,檢修時間1h,每維修一次閥門將導致充裝臺4h無法充裝,造成液氨積壓。
2、閥門泄漏的形式和原因分析
2.1、外漏
外漏是該閥的主要失效形式,占整個故障率的2/3。表現為球閥中分面泄漏、球閥尾端壓蓋泄漏和填料泄漏。外漏部位見圖1。
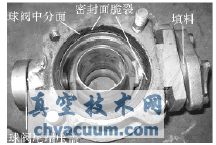
圖1 充氨閥外漏部位
1)密封墊材料選用錯誤。通過對泄漏閥門的拆檢,發現閥門中分面和球閥尾端壓蓋使用的密封墊發生硬化并冷脆斷裂,失去了密封墊應有的彈性,見圖1。
2)閥門結構不合理。閥座密封面直徑為102mm,加工了深4mm的密封槽,與之相配合的密封面外徑為110mm,聚四氟乙烯密封墊厚度5mm,墊片的有效壓縮量為1mm(圖2)。
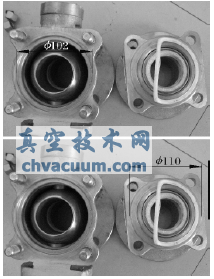
圖2 充氨閥密封部位
常溫下是能保證密封效果的,但在約-40℃的情況下使用,墊片因低溫收縮導致密封面緊力不夠從而發生泄漏。因上閥體密封面外徑(110mm)大于下閥體密封槽外徑(102mm),緊固連接螺栓時上、下閥體因密封面的尺寸設計缺陷而不能有效壓緊密封墊,出現上、下閥體連接螺栓擰得很緊而密封墊卻仍然未壓緊現象,這就是閥門中分面出現泄漏,通過緊固連接螺栓卻無法消除泄漏的根本原因。
2.2、閥門內漏
閥門內漏的主要原因是密封材料選擇錯誤所致。閥座密封墊脆裂導致泄漏是主要泄漏形式。主要原因是密封面材料選擇不合理,選用了常溫材料,致使墊片在低溫下失效脆裂,導致液氨泄漏,見圖3。
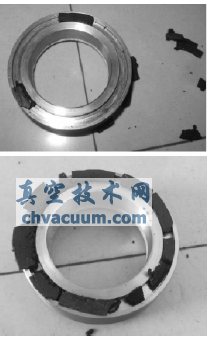
圖3 充氨閥閥座密封墊脆斷
3、解決對策
1)合理選擇密封墊材質。依據使用溫度和介質,球閥閥座密封材料、中分面密封材料、尾端壓蓋密封墊均采用聚四氟乙烯密封材料。聚四氟乙烯耐溫-180~250℃,耐壓-0.1~6.4MPa,在-20~250℃,允許驟冷驟熱,或冷熱交替操作,比較符合本充裝站的使用條件,是液氨球閥首選的密封材料。
2)對球閥上、下閥體密封尺寸作調整,準110mm的密封面加工至準100mm,使之能輕松壓入密封槽,保證能夠壓緊密封墊。
3)球閥填料選用膨脹石墨或聚四氟乙烯。
4)新到閥門拆檢,更換閥門中分面和球閥尾端壓蓋的密封墊為聚四氟乙烯墊。對上、下閥體密封尺寸作檢查確認。最后做水壓試驗,檢漏合格后方可使用。
5)盡量減少購買新閥門,對換下的舊閥門拆檢并更換密封墊,做水壓試驗,檢漏合格后備用,節約了檢修成本。
4、結束語
液氨充裝站Q47F-25P(DQ47F-25P)、DN50mm球閥經常發生外漏和內漏故障,雖更換前經常溫水壓試驗檢漏合格,但現場安裝使用中因工況變化易發生泄漏,最短的更換后3~4h即泄漏,嚴重影響正常充氨工作。通過對泄漏閥門解體檢查和分析,查明了泄漏的根本原因,通過對密封墊材質重新選材,墊片厚度和密封尺寸的調整,有效解決了泄漏故障。2011年修復換上的液氨球閥使用已經超過1a,至今未發生泄漏,證明處理措施是切實有效的。