基于有限元技術實現加氫閥閥體的結構設計
針對加氫閥高危工況,設計了閥體整體鍛造結構。針對閥體材料、流道形式、整體鍛造結構對閥體質量影響的復雜性,采用有限元分析軟件Patran進行強度分析,得到該閥體在最大工況時各個方向的應力和變形,驗證了閥體零件結構設計的合理性,為特殊閥門閥體的結構設計提供了一種方法,也為后續的優化設計工作提供了依據。
引言
加氫閥是用于介質中含有工業氫的易燃、易爆場合的特殊閥門。基于加氫閥的高危工況,目前國內石化行業基本采用進口高壓加氫閥門,為了加快國產加氫閥的進程,確保加氫閥的質量,采用先進的有限元技術對加氫閥關鍵零件如閥體進行結構設計顯得尤為必要。本文以某閘閥為例,依據API600等美國石油學會標準及以色列石油公司等客戶要求,提出了加氫閥閥體的結構設計方案,針對閥體材料、流道形式、整體鍛造結構對閥體質量影響的復雜性,利用SolidWorks建立了閥體的三維實體模型,給出了閥體最大工況時的邊界條件,使用有限元分析軟件MSC.Patran對其進行了強度分析,獲得該閥體在各個方向的受力和變形,得到閥體結構的最大應力部位,驗證了閥體零件設計的合理性。
1、閥體結構設計
1.1、基本參數
閘閥的技術參數如下:
公稱通徑:8英寸,即203.2mm;
公稱壓力:1500Lb,即25MPa;
適用溫度:-29℃~+427℃。
1.2、閥體材料及熱處理
在滿足氫腐蝕的基礎上,依據Couper曲線中高溫H2S+H2對各種鋼材的腐蝕率選擇適宜的閥體材料,如WC6(F11)、WC9(F22)、F321、F304、A105N等。依據ASMEB16.34及客戶訂單要求,加氫裝置閥門材料一般選用A105N、F22、F321。其中A105N材料的主要化學成分為:C的質量分數≤0.23%、P的質量分數≤0.035%、S的質量分數≤0.025%;其熱處理狀態為正火。F321的熱處理狀態為固溶+(850~870)℃正火處理。F22鍛件須為A182F22Class3,抗拉強度不超過690MPa,熱處理為正火+730℃回火。
1.3、閥體的結構
閥體采用整體鍛造結構,組織致密,表面質量好。閥體的流道采用全通徑式設計,其流道孔徑與閥門公稱通徑基本相同。閥體壁厚、閥體端法蘭、結構長度等結構尺寸設計依據API600《鋼制閘閥—法蘭連接或對焊端、螺栓連接閥蓋》及ASMEB16.34《閥門—法蘭連接端、螺紋連接端和對焊端》等標準的規定。
閥體零件圖如圖1所示。
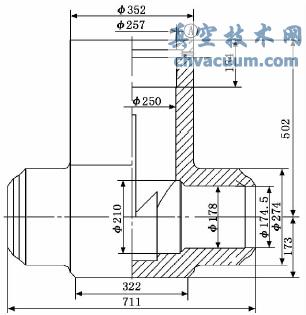
圖1 閥體零件簡圖
2、閥體有限元模型的強度分析
2.1、已知條件
加氫閥閥體的材料選用A105N,材料屈服強度≥250MPa,合格供應商材質報告中的屈服強度為360MPa,抗拉強度≥485MPa,彈性模量為202GPa,泊松比為0.30。
閥體內壓為25MPa。
2.2、邊界條件
(1)通道二端口焊接無限長管道尺寸為Φ219.1mm×Φ174.5mm。
(2)A-A自密封部位受25MPa內壓力以及閥蓋自密封產生的徑向分力2221.6kN,自緊密封圈對閥體的比壓為102.7MPa,閥蓋與閥體密封連接后,可作為中間剛性板。
(3)Tr270×6梯形螺紋面承受介質壓力為1276.8kN。
(4)5/8-11UNC螺紋處承受閘板關閉時的作用力為299.8kN。
(5)閥體中腔與通道交匯中心,受沿通道軸線方向閘板與閥座的密封力為402.6kN。
2.3 結構強度分析
2.3.1、閥體有限元模型的建立
加氫閥閥體零件為帶圓孔的鍛件結構,各連接處有過渡圓角、倒角,其結構相對復雜,所以在實體建模時應對模型進行必要的簡化。根據圣維南原理,對閥體的部分局部特征如倒(圓)角、螺釘孔等進行了適當的簡化,簡化后利用SolidWorks建立閥體的三維模型,如圖2所示。
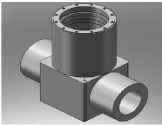
圖2 閥體三維模型圖
2.3.2、劃分網格
采用Patran中TetMesh網格生成器,用GlobalEdge Length方法控制網格的疏密,用10節點四面體單元劃分節點和單元,完成閥體網格的劃分。
2.3.3、加載位移和壓力的約束
按照邊界條件的要求,在MSC.Patran Loads/BCs模塊下完成閥體邊界條件的加載,并在Materials和Proper模塊下完成閥體材料彈性模量和泊松比的設定。加載完后的有限元模型如圖3所示。
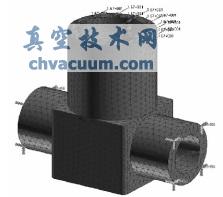
圖3 閥體有限元模型圖
2.3.4、結果求解
在Analysis模塊下,調用Nastran求解器進行線性求解,可得閥體的應力云圖,如圖4所示。
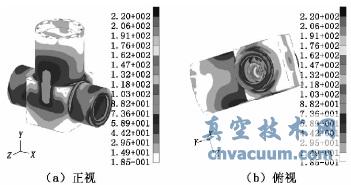
圖4 閥體應力云圖
3、結果分析
從圖4中可以清晰地發現,在載荷作用下,該零件工作時產生的最大應力為220MPa,低于材料的屈服極限250MPa,低于合格供應商材質報告中的屈服強度360MPa,其安全系數達到1.6;由圖4中還可看到,大部分應力在118MPa以下,只有在閥體中腔與通道交匯處產生了局部的應力集中,但低于材料的屈服極限250MPa。通過以上分析結果可以得出結論,該零件的結構合理,選擇的材料是可靠的,能夠承受工作時的載荷。
4、結束語
(1)基于有限元技術實現加氫閥閥體的結構設計,為現階段鍛鋼加氫閥國產化提供了一種方法,為我國多向模技術推廣提供了一種途徑。
(2)通過有限元分析可知該閥體零件工作時產生的最大應力為220MPa,低于材料的屈服極限250MPa,低于合格供應商材質報告中的屈服強度360MPa,可承受高壓負荷,滿足高危工況下的強度要求。
(3)針對閥體材料、流道形式、整體鍛造結構對閥體質量影響的復雜性,在加氫閥閥體結構設計過程中,引入有限元技術,為高溫高壓等環境苛刻條件下的產品結構設計提供了一種方法,也為后續的優化設計工作提供了依據。