閘閥閥座變形原因分析及改進措施
針對一起閘閥閥座變形失效事故,采用理論與試驗相結(jié)合的方法,對閘閥進行了宏觀分析、微觀分析、閥板厚度分析以及材質(zhì)理化性能檢驗。結(jié)果表明,閥板加工質(zhì)量差和閥座裝配不當導(dǎo)致閥座受到閥板大的擠壓力和摩擦力作用產(chǎn)生變形。提出了改進措施,取得了良好效果。
閘閥是一種使用廣泛的閥門,主要用來接通和截斷管路中的介質(zhì)。根據(jù)密封元件形式的不同閘閥可分為楔形閘閥、平行式閘閥、楔形雙閘板閘閥、平行雙閘板閘閥等。閘閥可采用自密封方式密封,也可采用強制密封。由于強制密封可靠性高,在石油化工行業(yè)使用較為普遍。
楔形閘閥靠楔形閥板上的兩密封面和閥座上的兩密封面楔入時的緊密結(jié)合來達到密封,由于楔入過程中密封面要承受大的擠壓力和摩擦力,所以密封面容易發(fā)生損傷而導(dǎo)致泄漏。為提高楔形閘閥的可靠性和延長其使用壽命,很多學(xué)者從材料、結(jié)構(gòu)和受力等方面進行了研究,但現(xiàn)場楔形閘閥失效事故仍時有發(fā)生,有些甚至在使用一次或幾次后就發(fā)生了失效,給生產(chǎn)帶來了很大的安全隱患。本文研究的失效閘閥為XFF65-60楔形閘閥,在油田現(xiàn)場第1次水壓試驗后就產(chǎn)生了失效。試驗中工作人員關(guān)閉閘閥后開啟,再次關(guān)閉閘閥后發(fā)現(xiàn)閘閥未能截止水流。本文以該起閘閥失效事故為研究對象,分析閘閥失效的原因,探討避免此類事故發(fā)生的措施和方法。
1、宏觀分析
剖開閘閥本體后發(fā)現(xiàn)閘閥內(nèi)部A閥座已發(fā)生大的變形(如圖1),A閥座局部內(nèi)凹、變形嚴重,左下側(cè)部位已脫離和本體的螺紋嚙合。
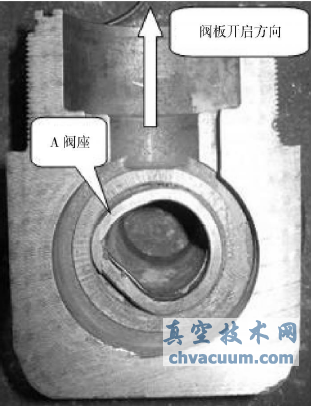
圖1 本體剖開后的A閥座外觀
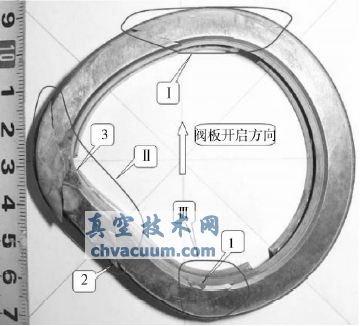
圖2 A閥座外觀形貌
A閥座外觀形貌如圖2,表面可見I、II和III三處破碎區(qū),表面硬化層和基體分界明顯;區(qū)域。兩條裂紋均從圓內(nèi)側(cè)貫穿到圓外側(cè),表面硬化層及附近基體有向閥板開啟方向較小的殘留位移;區(qū)域ò破碎嚴重,靠圓內(nèi)側(cè)裂紋處表面硬化層有脫落,表面可見3條從圓內(nèi)側(cè)貫穿到圓外側(cè)的裂紋,裂紋平行于閥板開啟方向,表面硬化層及附近基體有向閥板開啟方向的殘留位移;區(qū)域III裂紋呈90°三角形,自圓內(nèi)側(cè)兩處延伸相匯于端面中部,靠圓內(nèi)側(cè)裂紋處表面硬化層有脫落,表面硬化層及附近基體有向閥板開啟方向較小的殘留位移。
A閥座端面區(qū)域II和區(qū)域III局部破碎嚴重,區(qū)域II分布有2處發(fā)射狀小裂紋,顯示擠壓破碎形貌,區(qū)域II還可見從圓內(nèi)側(cè)點1到圓外側(cè)點2再到圓內(nèi)側(cè)點3的圓弧線擠壓痕跡(如圖2)。
B閥座變形成橢圓形,其中短軸方向平行于閥板開啟方向。閥板A面與A閥座密封面相接觸,外觀形貌如圖3,區(qū)域。倒角處有粘結(jié)金屬粒。閥板B面完好,未見損傷。
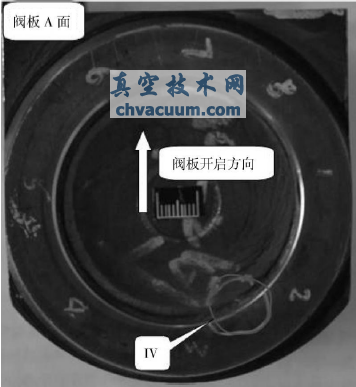
圖3 閥板A面外觀形貌
2、閥座表面微觀分析
對圖2中的區(qū)域II進行電子顯微鏡觀察,如圖4,可見裂紋以集中區(qū)(圖中雙點劃線圓)為中心呈放射狀擠壓破碎形貌,所以區(qū)域ò受到了局部擠壓作用。對區(qū)域II平整處顯微觀察發(fā)現(xiàn)有摩擦損傷形貌(如圖5)。
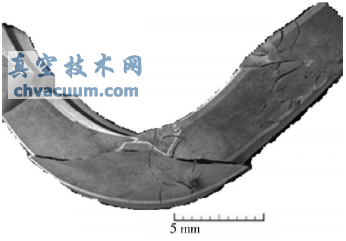
圖4 A閥座區(qū)域II微觀形貌
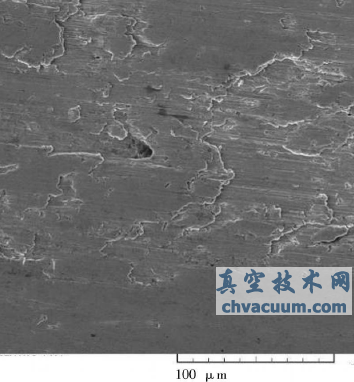
圖5 A閥座區(qū)域II表面摩擦形貌
3、閥板厚度分析
將閥板密封環(huán)中心圓均勻分成16等份按圖3方位進行厚度測量,最下端為起始零點,按逆時針方向逐一測量。以密封環(huán)中心圓方位角為橫坐標,以測量點厚度值為縱坐標畫折線圖(如圖6)。由圖6可見,密封環(huán)中心圓對稱位置處厚度有較大差異,呈現(xiàn)不對稱性,另外180b方位處(圖3最上端)厚度明顯偏小,這將嚴重影響閥板和閥座貼合的緊密度,閥板開啟和關(guān)閉過程中在2對接觸面上必將產(chǎn)生大的摩擦阻力。
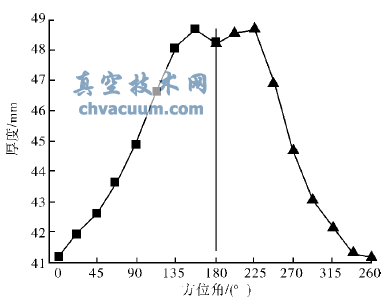
圖6 閥板密封環(huán)沿圓周厚度值
4、材質(zhì)分析
對閥座、閥板和本體進行化學(xué)成分分析,對本體進行縱向拉伸和橫向沖擊試驗,結(jié)果符合SY/T5127-2002標準和廠家規(guī)范要求。對閥座基體進行金相分析,結(jié)果如下:組織為珠光體和鐵素體(如圖7);組織晶粒度為10.5級;夾雜物為A2.0,B0.5,DTiN1.5。
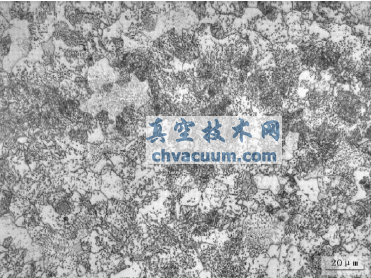
圖7 閥座顯微組織
5、綜合分析
A閥座硬化層有3處破碎區(qū),嚴重破碎區(qū)域II主裂紋貫穿整個硬化層,主裂紋附近分布有縱多微小裂紋;宏觀觀察發(fā)現(xiàn)區(qū)域II破碎區(qū)裂紋以集中區(qū)為中心呈擠壓破碎形貌,區(qū)域II宏觀可見擠壓殘留的圓弧線痕跡,微觀觀察可見表面摩擦形貌;A閥座3處破碎區(qū)表面硬化層及附近基體有向閥板開啟方向的殘留位移。B閥座變形呈橢圓形,其短軸方向平行于閥板開啟方向。據(jù)上推測,A閥座和B閥座都受到了大的擠壓力和摩擦力作用,其中摩擦力方向平行于閥板開啟方向。
如果A閥座和B閥座裝配后的兩表面楔形間距過大,閥板在閥桿的帶動下可移動到本體內(nèi)部最底端(如圖8b)。正常情況下,閥座下邊緣離本體內(nèi)部空間最下端距離為20mm(如圖8c),而閥板在極限位置時的接觸面內(nèi)圓最下邊緣離本體內(nèi)部空間最下端距離為17mm(如圖8b),所以閥板在圖8b極限位置開啟上移過程中下部內(nèi)倒角邊沿會刮蹭到閥座下半部分,致使閥座變形或使表面破碎的小塊剝落。A閥座嚴重破碎區(qū)和閥板A面粘結(jié)金屬區(qū)方位呈對稱性,說明這2處是閥座和閥板密封接觸時的對應(yīng)部位,此現(xiàn)象及A閥座和B閥座的變形方向證明了上述情況的發(fā)生。
綜合以上分析,推斷A閥座在受到閥板擠壓摩擦后產(chǎn)生了變形和硬化層局部的破碎,閥板在本體內(nèi)部過極限位置開啟上移過程中致使閥座變形以及表面硬化層的進一步破碎和剝落。
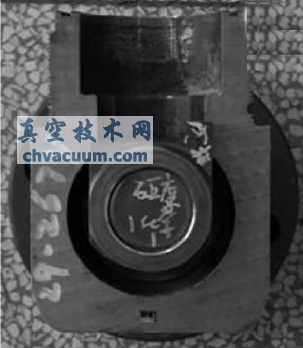
a 閥板正常位置
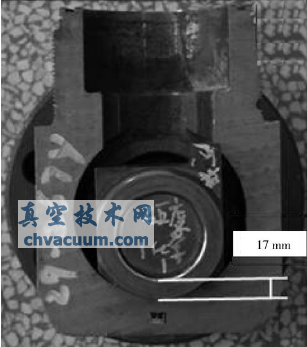
b 閥板極限位置
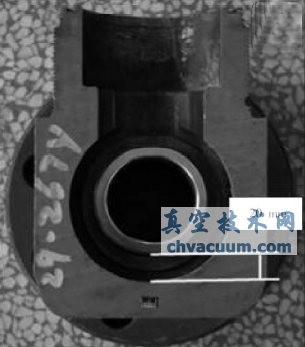
c 閥座正常位置
圖8 閥板極限位置示意
6、改進措施及效果
a)改進閥板兩環(huán)形密封面的加工工藝,在保證兩密封面平面度的同時保證兩密封面的對稱性。
b)安裝新的閥座,調(diào)整閥座兩密封表面間楔形空間至閥板移動到預(yù)定位置時達到良好密封。
c)加強對使用前和使用后閘閥的檢測,避免有損傷或存在其他缺陷的閘閥進入現(xiàn)場使用。
d)安裝新的閥板和閥座后重新對閘閥進行水壓試驗,結(jié)果合格,后期油田現(xiàn)場對閘閥開啟和關(guān)閉32次也未發(fā)現(xiàn)閘閥發(fā)生泄漏或損壞。
7、結(jié)論
1)閥板兩側(cè)楔形表面平面度差,兩側(cè)平面與中心面不對稱,嚴重影響了閥板和閥座的密封性能,并且導(dǎo)致閥板楔入和開啟過程中對閥座表面產(chǎn)生過大的局部擠壓力和摩擦力。
2)A閥座和B閥座裝配位置不當導(dǎo)致兩密封表面間楔形空間過大,閥板移動到預(yù)定位置時和閥座不能產(chǎn)生緊密密封。
3)A閥座和B閥座受到閥板大的擠壓力和摩擦力作用導(dǎo)致變形。
4)改進后的閥座滿足了使用要求。