L型進(jìn)渣閥進(jìn)渣特性試驗(yàn)研究
在L型進(jìn)渣閥半工業(yè)試驗(yàn)臺(tái)上,針對(duì)表觀引渣風(fēng)風(fēng)速在0~25m/s、引渣風(fēng)管深入比例0~0.6、聯(lián)箱壓力0.05~0.15MPa、試驗(yàn)物料粒徑1.32 ~2.22mm時(shí),對(duì)該進(jìn)渣閥的進(jìn)渣特性進(jìn)行了試驗(yàn)研究。試驗(yàn)結(jié)果表明:隨著表觀引渣風(fēng)風(fēng)速增大,進(jìn)渣閥進(jìn)渣速率先增大后減小;進(jìn)渣速率隨引渣風(fēng)管深入比例的增大、試驗(yàn)床料顆粒平均粒徑的增大而減小,隨聯(lián)箱壓力的增大而增加。此外,還得到了進(jìn)渣特性的關(guān)聯(lián)式,關(guān)聯(lián)式的計(jì)算值與測(cè)量值吻合較好,可用于指導(dǎo)進(jìn)渣閥的調(diào)節(jié)。
引言
循環(huán)流化床鍋爐的穩(wěn)定運(yùn)行需要合適且穩(wěn)定的爐膛床壓以及正常的流化,而爐膛床壓的控制是通過爐膛底部排放底渣來實(shí)現(xiàn)的,同時(shí)從爐膛底部排出粗顆粒及焦塊以防止進(jìn)一步的結(jié)焦。當(dāng)鍋爐燃用煤種為低熱值煤種時(shí),其灰分通常占到40%-60% ,甚至更高。由于CFB鍋爐底渣含有大量的物理熱,因此當(dāng)灰渣不經(jīng)過冷卻直接排出時(shí),灰渣物理熱損失可超過3%。如果灰渣物理熱采用汽機(jī)冷凝水冷卻回收,又會(huì)因排擠抽汽而帶來較大的汽機(jī)側(cè)冷源熱損失。因此在CFB鍋爐燃燒劣質(zhì)煤時(shí),應(yīng)盡量采用流化床冷渣器,通過空氣和高壓給水吸熱,將底渣物理熱回收到鍋爐中。為此,課題組開發(fā)了混流式流化床冷渣技術(shù),并已投入工業(yè)應(yīng)用。該冷渣器配有一種在結(jié)構(gòu)上可調(diào)節(jié)的L型進(jìn)渣閥,該進(jìn)渣閥是在常規(guī)L閥的基礎(chǔ)上加裝可伸縮的噴氣管而形成的,其基本工作原理與L閥相同,但工作特性有所不同,主要不同點(diǎn)在于:該L閥處理的不是細(xì)顆粒,而是較粗的鍋爐底渣。
國(guó)內(nèi)外學(xué)者對(duì)對(duì)L閥的研究較多,但主要集中在粒徑小于90μm的Geldart-A類顆粒和90~650μm的Geldart-B類顆粒,而對(duì)于顆粒尺寸及密度較大的Geldart-D類顆粒的研究則很少。但實(shí)際循環(huán)流化床鍋爐排出的底渣則是具有寬篩分特性的顆粒,D類顆粒所占比例可達(dá)50%乃至更高。
為進(jìn)一步掌握該進(jìn)渣閥在處理底渣床料時(shí)的氣固流動(dòng)特性,本研究對(duì)混流式流化床冷渣器配套的進(jìn)渣閥的氣固流動(dòng)特性進(jìn)行了較系統(tǒng)的試驗(yàn)研究,其研究結(jié)果也可用于其它類似系統(tǒng)的進(jìn)渣控制。
1、試驗(yàn)系統(tǒng)
1.1、試驗(yàn)系統(tǒng)
試驗(yàn)系統(tǒng)由3部分組成: 試驗(yàn)臺(tái)本體、送風(fēng)系統(tǒng)和試驗(yàn)數(shù)據(jù)采集系統(tǒng)。
試驗(yàn)臺(tái)本體包括立管、排渣導(dǎo)管、引渣風(fēng)管、冷渣器本體、排渣稱重盒。立管直徑219mm,高600mm;排渣導(dǎo)管直徑159mm,長(zhǎng)400mm。數(shù)據(jù)采集系統(tǒng)包括采集壓力分布的KYB14A型差壓變送器、Adam4117型號(hào)壓力模塊、Adam4520 型號(hào)轉(zhuǎn)換模塊及工業(yè)計(jì)算機(jī)。試驗(yàn)系統(tǒng)如圖1所示。
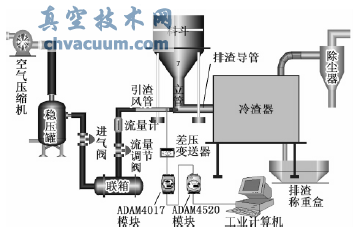
圖1 冷態(tài)試驗(yàn)裝置系統(tǒng)
1.2、試驗(yàn)物料及方法
試驗(yàn)物料采用引進(jìn)技術(shù)制造的某300MWCFB鍋爐底渣,粒徑范圍0~20mm,堆積密度1430kg/m3,真實(shí)密度2419kg/m3,平均粒徑1.32mm。試驗(yàn)物料粒徑分布如圖2所示。
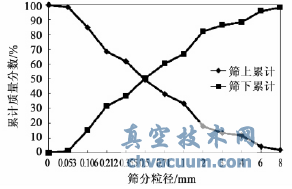
圖2 試驗(yàn)物料篩分特性曲線
試驗(yàn)過程中,分別調(diào)節(jié)引渣風(fēng)管噴嘴出口處的表觀引渣風(fēng)風(fēng)速、引渣風(fēng)管在閥體內(nèi)的深入比例(即引渣風(fēng)管深入閥體立管段的長(zhǎng)度與立管直徑的比值,如圖1中深入比例XL=0.5) 、引渣風(fēng)來流處聯(lián)箱壓力和試驗(yàn)物料平均粒徑。試驗(yàn)時(shí)間30~60s。數(shù)據(jù)采集系統(tǒng)記錄各試驗(yàn)工況的時(shí)間和壓力,進(jìn)渣量由排渣稱重盒稱取,并反復(fù)進(jìn)行多次試驗(yàn),在進(jìn)行方差檢驗(yàn)后對(duì)實(shí)驗(yàn)結(jié)果取平均值以便計(jì)算進(jìn)渣速率。
2、進(jìn)渣特性的試驗(yàn)結(jié)果及分析
2.1、表觀引渣風(fēng)風(fēng)速對(duì)進(jìn)渣特性的影響
圖3為引渣風(fēng)管深入比例分別為0、0. 2、0.4時(shí)的表觀引渣風(fēng)風(fēng)速對(duì)進(jìn)渣特性的影響。引渣風(fēng)管深入比例為零時(shí),當(dāng)表觀風(fēng)速達(dá)到7.37m/s時(shí)系統(tǒng)開始進(jìn)渣。隨表觀風(fēng)速增加,進(jìn)渣速率增大。當(dāng)表觀風(fēng)速為15.98m/s時(shí),進(jìn)渣速率達(dá)到最大值8.46kg/s。隨著表觀風(fēng)速的進(jìn)一步增大,進(jìn)渣速率開始逐漸減少,最終穩(wěn)定在7.15kg/s。即存在一個(gè)轉(zhuǎn)折風(fēng)速,表觀風(fēng)速小于該轉(zhuǎn)折風(fēng)速時(shí),進(jìn)渣速率隨表觀風(fēng)速的增加而增加; 表觀風(fēng)速大于該轉(zhuǎn)折風(fēng)速時(shí),進(jìn)渣速率隨表觀風(fēng)速的增加而減小。引渣風(fēng)管深入比例為0.2~0.4時(shí)也同樣存在轉(zhuǎn)折風(fēng)速,其值分別為11.05和9.21m/s。存在轉(zhuǎn)折風(fēng)速的原因在于:進(jìn)渣閥在運(yùn)行時(shí),進(jìn)渣所需要的壓頭由立管段的料位提供,該壓頭存在一個(gè)最大值,其值為該料位下的床料處于臨界流化時(shí)對(duì)應(yīng)的床層壓降。在本試驗(yàn)中,料斗的截面尺寸為1.2×0.8m,立管段的直徑為0.219m,在試驗(yàn)過程中料斗料位高度變化不超過0.2m。根據(jù)張偉等人的研究,此時(shí)料位波動(dòng)對(duì)進(jìn)渣速率的影響很小;而隨著表觀風(fēng)速的增大水平管段的阻力是逐漸增加的,這就導(dǎo)致了該進(jìn)渣速率在隨表觀風(fēng)速增加的過程中存在一個(gè)最大值。另外,隨著深入比例的增加,所需的啟動(dòng)表觀風(fēng)速及最大進(jìn)渣速率值均減小。
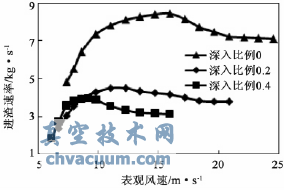
圖3 進(jìn)渣速率與觀引渣風(fēng)風(fēng)速的關(guān)系曲線
2.2、引渣風(fēng)管深入比例對(duì)進(jìn)渣特性的影響
表觀引渣風(fēng)風(fēng)速分別為7.37、8.6、9.82和11.05m/s時(shí)引渣風(fēng)管深入比例對(duì)進(jìn)渣特性的影響如圖4所示。由圖可見,隨著引渣風(fēng)管深入比例的增加,引渣風(fēng)管噴嘴前端可被吹動(dòng)的物料量減少,閥體內(nèi)因不易流動(dòng)所引起的死區(qū)所占比例增大,因此進(jìn)渣速率大體上呈現(xiàn)出減小的趨勢(shì)。但在表觀引渣風(fēng)風(fēng)速較小為7.37m/s時(shí),進(jìn)渣速率先減小后增加而后又減少。這是由于在引渣風(fēng)管深入比例的增加的同時(shí),試驗(yàn)物料在水平管段中運(yùn)動(dòng)所受到的阻力也在相應(yīng)地減小。
2.3、聯(lián)箱壓力對(duì)進(jìn)渣特性的影響
圖5為聯(lián)箱壓力分別為0.05、0.1和0.15MPa時(shí)進(jìn)渣特性曲線圖。隨著聯(lián)箱壓力的增大,進(jìn)渣速率呈現(xiàn)出不同程度的增加。主要原因是:當(dāng)聯(lián)箱壓力變大而流量保持不變時(shí),由于管路的沿程阻力損失是一定的,因此引渣風(fēng)的壓頭變大,引渣風(fēng)氣流的動(dòng)量增大、剛性增強(qiáng),其攜帶能力增強(qiáng),導(dǎo)致進(jìn)渣速率增加2~15%不等。在表觀引渣風(fēng)風(fēng)速越大時(shí),聯(lián)箱壓力對(duì)進(jìn)渣特性的影響更為顯著。
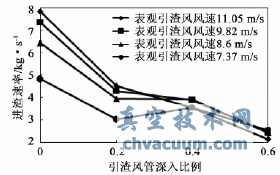
圖4 進(jìn)渣速率與引渣風(fēng)管深入比例的關(guān)系曲線
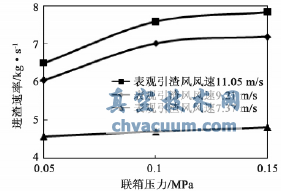
圖5 進(jìn)渣速率與聯(lián)箱壓力的關(guān)系曲線
2.4、顆粒物性對(duì)進(jìn)渣特性的影響
圖6為顆粒粒徑分別為1.32、1.92和2.22mm時(shí)的進(jìn)渣特性曲線。表觀引渣風(fēng)風(fēng)速相同時(shí),隨著試驗(yàn)床料中4mm以上粗顆粒含量的增加,試驗(yàn)物料的平均粒徑由1.32mm增大至2.22mm,氣流與固體顆粒之間的物性差異增大,氣流在延伸和前進(jìn)過程中的動(dòng)量消耗增加,氣流動(dòng)量及剛度減小,因此在相同表觀引渣風(fēng)風(fēng)速下所能獲得的進(jìn)渣速率減小。另外由于不同顆粒平均粒徑下的最大進(jìn)渣速率由8.46降至5.62kg/s,對(duì)應(yīng)轉(zhuǎn)折風(fēng)速也相應(yīng)地由15.96減少到12.28m/s。
2.5、進(jìn)渣特性的關(guān)聯(lián)式
試驗(yàn)表明,影響進(jìn)渣閥進(jìn)渣特性的因素有:表觀引渣風(fēng)風(fēng)速υ、引渣風(fēng)管深入比例XL、引渣風(fēng)來流聯(lián)箱壓力p、顆粒平均粒徑dp、轉(zhuǎn)折風(fēng)速vmf。通過無量綱分析,可確定進(jìn)渣特性關(guān)聯(lián)式為:

式中:GP—進(jìn)渣速率,ρg—氣體密度,D—進(jìn)渣閥立管段直徑,υ—氣體運(yùn)動(dòng)粘度,ν—表觀引渣風(fēng)風(fēng)速,νmf—轉(zhuǎn)折風(fēng)速,p—引渣風(fēng)來流聯(lián)箱壓力,p0—大氣壓,XL—引渣風(fēng)管深入比例,dp—顆粒平均粒徑,A、a、b、c、d均為常數(shù)。
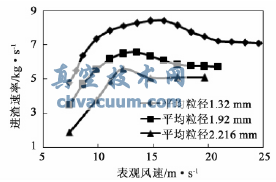
圖6 不同顆粒平均粒徑下的進(jìn)渣特性曲線
通過對(duì)轉(zhuǎn)折速度進(jìn)行擬合,發(fā)現(xiàn)該轉(zhuǎn)折速度與引渣風(fēng)管深入比例及顆粒平均粒徑有關(guān),因此擬合得到轉(zhuǎn)折風(fēng)速的關(guān)聯(lián)式為:

將實(shí)驗(yàn)數(shù)據(jù)代入式(1)進(jìn)行回歸,得到進(jìn)渣特性關(guān)聯(lián)式為:
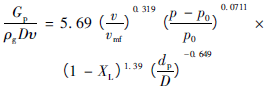
公式(3)的適用范圍:
表觀引渣風(fēng)風(fēng)速ν:6.14~24.56m/s
顆粒平均粒徑dp:1.32~2.216mm
聯(lián)箱壓力p:0.05~0.15MPa
渣溫:室溫
圖7為進(jìn)渣速率GP的計(jì)算值與測(cè)量值的比較。結(jié)果表明,式(3)的擬合相關(guān)度較好,誤差在25%以內(nèi)。
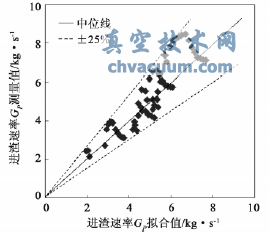
圖7 Gp擬合值與測(cè)量值的比較
3、結(jié)論
(1)試驗(yàn)表明隨著表觀引渣風(fēng)風(fēng)速的增大,進(jìn)渣閥的進(jìn)渣速率呈現(xiàn)出先增大后減小的趨勢(shì),即存在一個(gè)轉(zhuǎn)折速度,在該速度下可獲得更經(jīng)濟(jì)的進(jìn)渣速率。實(shí)際運(yùn)行中表觀引渣風(fēng)風(fēng)速的選取可以將轉(zhuǎn)折速度作為參考依據(jù);
(2)隨著引渣風(fēng)管深入比例的增大、顆粒平均粒徑的增大,進(jìn)渣速率減小; 隨著聯(lián)箱壓力的增大,進(jìn)渣速率逐漸增加,且表觀引渣風(fēng)風(fēng)速越大時(shí)更為顯著;
(3)對(duì)試驗(yàn)數(shù)據(jù)進(jìn)行多元回歸分析,分析得到了進(jìn)渣閥進(jìn)渣特性的關(guān)聯(lián)式。關(guān)聯(lián)式計(jì)算值與測(cè)量值吻合較好,可用于相應(yīng)參數(shù)條件下進(jìn)渣速率的計(jì)算,為進(jìn)渣特性提供了理論依據(jù)。
由于電廠現(xiàn)場(chǎng)的壓縮空氣壓力通常在0.5~0.7MPa左右,而且底渣的溫度高達(dá)850℃甚至更高,因此在更高壓力引渣風(fēng)條件及高溫條件下的進(jìn)渣閥的氣固流動(dòng)特性,還需要進(jìn)一步的試驗(yàn)研究。