鍋爐減溫減壓控制系統的改造與實現
基于對鍋爐減溫減壓控制系統不穩定的原因分析,從控制系統的硬件和軟件兩個方面,對容易損壞的部分進行技術性變革。整個系統結構簡單,提高了控制系統的可靠性,最大限度地減少系統故障,對安全、高效生產有現實意義。
工藝參數的穩定可靠是保證產品質量的重要前提。某輪胎公司目前半鋼產量約為15000套/天,半鋼生產過程硫化工藝所需內壓蒸汽的連續供給,平常是由動力廠熱電站汽輪機一級抽汽得到,而在汽輪機不能正常運行時,由雙減系統將鍋爐出口過熱蒸汽經減溫減壓后對外供汽。由于執行機構工作環境惡劣,系統干擾因素太多,容易引發控制失靈,最終導致工藝參數超標。而這種故障發生具有突發性和危害性大的特點,因此,如何改善雙減系統控制品質,消除控制系統故障,使其運行可靠,成為設備改造的重點課題。
1、減溫減壓控制系統缺陷分析
目前雙減控制系統工作的模式是:鍋爐供給壓力為3.2~3.6MPA、溫度為420℃~445℃的過熱蒸汽,經雙減調節閥減溫減壓后成為壓力在1.47~1.52Mpa、溫度在230℃~240℃范圍的外供蒸汽,其壓力和溫度控制是由傳感器測量壓力、溫度信號后經配電器進S9000控制器,由控制器發出控制信號通過手操器對現場調節閥進行控制。
針對可能導致控制系統不穩定的各環節的現場深入分析:現場環境溫度長期高達60多度,電子元件容易老化;信號傳輸路線長,經過發電機、配電室等強電區域,容易產生干擾信號;同時調節閥工作前后壓差大,使用時間年久,導致閥門卡澀、泄漏量大、動作不靈敏甚至誤動作等。多種因素將導致經常出現系統控制失靈,輕者半鋼硫化車間出現成批廢次品,嚴重時不得不停產。
2、減溫減壓控制系統的技術改造與實現
根據對雙減控制系統不穩定的原因分析,我們將容易損壞的部分進行技術性變革,提高雙減裝置的工作效率,確保鍋爐安全、經濟、穩定運行。
2.1、更換新型配電器
原配電器電路設計不合理,聯結部份采用焊接結構,容易產生接觸不良;電子元件溫度漂移使得準確度下降,針對這種情況,我們重新選購了電路設計合理、便于維修更換(插拔式)能夠減少維修時間的新型號配電器,同時將配電器、壓力變送器的校驗周期由原來一年一次改為2個月一次,保證了參數測量的精確度。
2.2、改進聯軸器結構
原電動執行機構生產廠家設計的聯軸器是整體式,且固定螺栓只有2個,絲牙容易損壞,而一旦絲牙損壞更換非常麻煩;經過重新測量尺寸繪圖加工后,改為由兩塊組成,將聯軸器的固定螺栓由2個增加為4個,外加并帽,并定期檢查固定螺栓松緊程度。
2.3、環境溫度高及強電干擾的應對措施
由于現場環境惡劣,環境溫度高,特別是夏季,可達到60多度,幾乎工作在儀表技術參數的極限范圍(-25℃~70℃)電子元件長期工作與此環境下,極易老化,從而穩定性急劇下降;另外我們發現伺服電機的絕緣性能也已下降,極易燒毀。對此,我們仔細測試了現場儀表上的每個電子元件的性能,對于技術參數指標有所偏差可能的不良元件全部予以了更換;對伺服電機,將相關技術參數提供給馬達組由其重新繞制,經裝配、接線、調試運行試驗證明完全可以代替使用;傳輸信號經過發電機和配電室等強電區域,易產生干擾信號,我們對系統每個環節進行了逐一檢查,改變了局部電纜走向,將不是屏蔽的電纜改為屏蔽電纜,并保證接地牢靠。
2.4、對控制系統失靈的改進
雙減控制系統的工作原理是:壓力控制是由壓力變送器檢測壓力信號后經配電器進S9000控制器,由S9000控制器發出控制信號通過手操器和執行機構反饋來的閥門位置反饋信號進行運算后,直接輸出正反轉信號驅動電動執行機構電機,控制電機正反轉,而電機正反轉動作帶動調節閥閥桿上下運動,從而改變蒸汽閥門開度,起到調節壓力作用;值得一提的是,此調節閥與一般調節閥結構不同,閥門底部加入減溫水在閥門內與蒸汽混合,其減溫水量由減溫調節閥出口控制。其溫度、壓力控制原理圖如圖1所示。
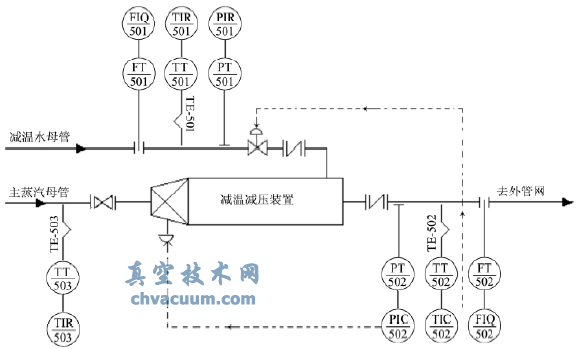
圖1 雙減溫度、壓力控制系統圖
雙減溫度、壓力控制原理方框圖如圖2所示。由于閥門前后壓差大,用戶負荷變化不定,用人工調節難以達到工藝指標。為了保證核心部件控制器可靠性,我們進行了下列幾方面的改造:
①將易導致故障的邏輯處理器Run/Disable鑰匙轉換開關改成跳線轉換;②將與上位機通訊的接頭固定牢靠;③為了以防萬一,決定增加一套后備自動調節系統。即增加兩臺單回路智能調節器和兩個轉換開關,改變系統接線方式,當S9000控制失靈時切換轉換開關,投入智能調節器控制。改造后控制系統圖示如圖3所示。
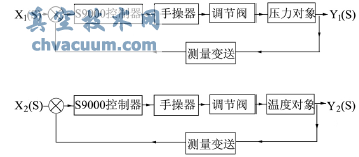
圖2 雙減溫度、壓力控制原理方框
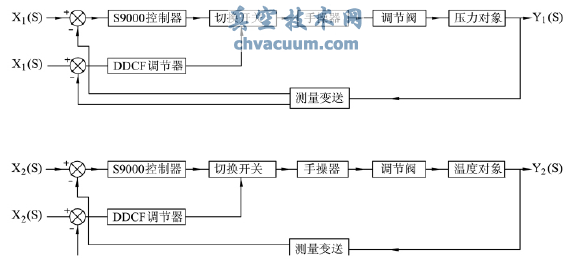
圖3 改造后的雙減溫度、壓力控制原理方框圖
2.5、調整電動執行機構
對電動執行機構進行拆檢,我們發現渦輪渦桿機構滾珠行程軌道不光滑,部分滾珠磨損嚴重,更換所有的滾珠,打磨不平軌道,改用耐高溫的鋰基脂作為轉動部件潤滑油;對閥門和電動執行機構進行重新組裝,保證既能滿足工藝需要,又能符合調節要求,合理調整剎車機構松緊程度;改變手操器的設定參數,不斷修正執行機構動作靈敏度,使其既能不可能發生卡澀又不易造成振蕩而失控現象。
2.6、重新整定控制參數
根據自動控制理論,由于壓力測點裝在減壓閥后不遠的地方,壓力變化時反應較快,即壓力調節對象的滯后時間很小,上升速度很快,因此,整定調節參數時,放大倍數應設置得大一些,積分時間小一些,由于微分作用對快速調節對象的反應敏感,一般不采用微分作用,理論要求放大倍數K=2.5~5,積分時間Ti=5~10秒;而減溫通過減溫水來控制,溫度測點離噴水點距離較近,K=2.5~5之間,Ti=10~20秒,Td=(1/2~1/3)Ti,由于壓力變化對溫度影響較大,投好壓力自動調節有利于溫度控制質量的提高。根據這一理論的指導,結合我們的實際工況,經過我們幾個班次跟蹤設備的運行,不斷摸索,終于得到最佳的的PID控制參數,使得系統不僅控制及時、而且無振蕩,壓力和溫度精度得到提高。
2.7、調整運行工作方式
由于閥門長期使用后有一定的泄漏量,使得在低負荷時閥門工作特性較差,從而影響控制質量,此時我們要求運行人員合理地開大另一臺雙減調節閥,以增大該雙減調節閥的負荷,(另一臺雙減調節閥安裝在該雙減調節閥后,是后者的一個分支,提供9公斤蒸汽,此蒸汽通常由發電機背壓排汽得到,若另一臺雙減調節閥開得太大,勢必影響發電機發電量,這樣就不能達到經濟運行),實踐證明,此項措施非常有效。
3、小結
經過對雙減控制系統的改進與反復調試,生產自動過程得以實現,從改造后近兩年的運行情況看,生產效率明顯提高,極大地提高了鍋爐蒸汽供給系統的穩定性和可靠性,具有顯著的特色和很大的實用價值。至今的生產運行狀況來看,已取得了顯著效益:
(1)此改造項目,總投資約5000元人民幣,主要用于購買4臺單回路PID調節器、配電器、部分電子元件等,其余材料均就地取材,減少了投資,節約了維修費用。
(2)徹底消除了閥門的卡澀,排除了因閥門的不正常開關給鍋爐和壓力管道帶來的安全隱患。
(3)改造后,未出現因設備故障而導致工藝參數超標、半鋼車間因此而出現廢次品,更未因此而停產,保障了正常連續生產。