一起高壓雙閥聯(lián)體閥焊縫撕裂未遂事件的分析及防范對(duì)策
未遂事件和傷害事故具有相同的機(jī)理和誘因,經(jīng)過對(duì)新建220×104t/a蠟油加氫處理裝置開工生產(chǎn)過程中出現(xiàn)的一起高壓雙閥聯(lián)體閥焊縫撕裂未遂事件,對(duì)誘發(fā)原因進(jìn)行深度剖析,提出相應(yīng)的對(duì)策和建議,從而避免同類事故的發(fā)生。
1、蠟油加氫處理裝置簡(jiǎn)介
1.1、工藝簡(jiǎn)介
某公司220×104t/a蠟油加氫處理裝置以減壓蠟油、焦化蠟油和脫瀝青油的混合油為原料,其中減壓蠟油進(jìn)料為76.21wt%,焦化蠟油進(jìn)料為13.82wt%,脫瀝青油進(jìn)料為9.97wt%,進(jìn)料硫含量為1.73m%,采用撫順石油化工研究院(FRIPP)開發(fā)的FFHT蠟油加氫處理工藝技術(shù),加氫處理催化劑采用FRIPP的FF-18(保護(hù)劑為FZC系列保護(hù)劑) 。主要生產(chǎn)硫含量低于1700μg/g的精制蠟油,為催化裂化裝置提供優(yōu)質(zhì)的原料,同時(shí)副產(chǎn)少量石腦油和柴油。
1.2、潛在的危險(xiǎn)
蠟油加氫處理裝置是高溫高壓、高硫化氫、臨氫裝置,反應(yīng)器設(shè)計(jì)壓力12.81MPa,設(shè)計(jì)溫度450℃,循環(huán)氫中硫化氫含量高達(dá)10000μg/g。反應(yīng)器內(nèi)的主導(dǎo)化學(xué)反應(yīng)為放熱反應(yīng)。一旦設(shè)備密封及質(zhì)量出現(xiàn)問題容易引起油氣泄漏,引發(fā)火災(zāi)爆炸和硫化氫中毒事故,若在高低分離區(qū)操作不當(dāng),則極易造成油氣互竄和高低壓互竄,從而引發(fā)設(shè)備爆炸事故。
2、未遂事件剖析
2.1、事件簡(jiǎn)要經(jīng)過
2009年5月18日凌晨4:40,當(dāng)班兩位操作人員在裝置現(xiàn)場(chǎng)檢查中,身上的硫化氫報(bào)警儀突然報(bào)警,迅速撤離人員。在穿戴好防護(hù)用品后到現(xiàn)場(chǎng)查找泄漏點(diǎn),發(fā)現(xiàn)反應(yīng)器R5101的冷氫線流量孔板引壓雙聯(lián)閥前焊縫開裂,壓力為10.0MPa、硫化氫濃度為10000μg/g的氫氣大量泄漏。如不及時(shí)采取措施,很可能引發(fā)一起嚴(yán)重的硫化氫中毒、氫氣泄漏著火爆炸的惡性事故。在向上級(jí)報(bào)告的同時(shí),迅速采取系統(tǒng)降壓、隔離泄漏點(diǎn)、切斷泄漏源等措施,控制了事態(tài)的進(jìn)一步擴(kuò)大。由于兩位操作員發(fā)現(xiàn)及時(shí),處理得當(dāng),避免了一起可能發(fā)生的重大火災(zāi)爆炸、中毒事故。
2.2、事件原因分析
(1)該批閥門主要用于加氫處理裝置儀表引壓一次閥門或儀表放空、排凝閥門,共83只,其中A105(碳鋼)材質(zhì)的62只,321(0Cr18Ni10Ti)材質(zhì)的19只,F(xiàn)11(12Cr1MoV)材質(zhì)的2只。5月18日,由檢修公司理化組對(duì)該批83只閥門的166道閥體焊縫進(jìn)行著色檢驗(yàn),發(fā)現(xiàn)有12處焊縫缺陷,其中有氣孔、焊縫余高不足和咬邊的缺陷,其中A105焊縫4道,321焊縫6道,F(xiàn)11焊縫2道,5月20日對(duì)排查出的12處缺陷進(jìn)行補(bǔ)焊處理。(見圖1、圖2)
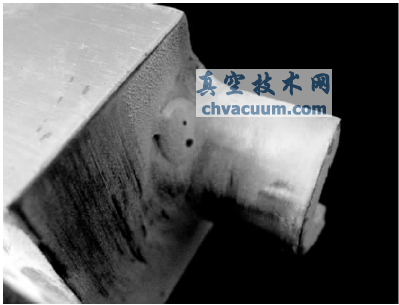
圖1 焊縫上的氣孔
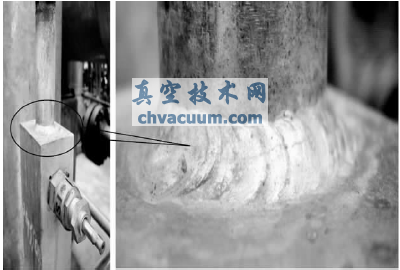
圖2 焊縫余高不足和咬邊缺陷
(2)為保證裝置的安全運(yùn)行,由檢修公司理化組將此閥門刨開進(jìn)行檢驗(yàn)。從刨開的閥門看,閥門接管承插焊接部位的焊肉太小,刨開實(shí)測(cè)最小位置為2.8mm,且閥門承插焊接焊縫存在有氣孔等缺陷。(見圖3、圖4)
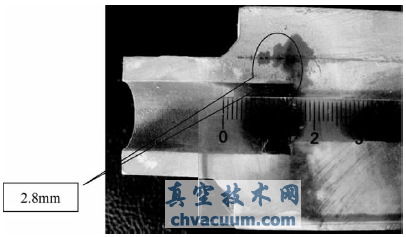
圖3 閥門承插焊接的接管焊肉高度
(3)初期檢查不到位。在裝置開工三查四定期間,由于時(shí)間緊、人員少等各種原因,對(duì)裝置設(shè)備的部分細(xì)節(jié)檢查不到位,沒有及時(shí)發(fā)現(xiàn)設(shè)計(jì)、施工的漏洞和缺陷,從而間接地造成了此次泄漏事故的發(fā)生。
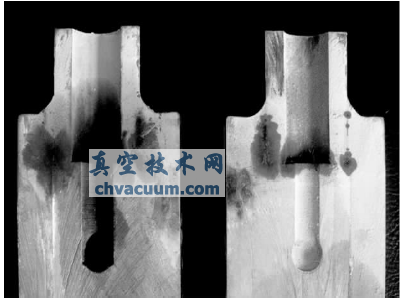
圖4 閥門承插焊接的接管
(4)從閥門的設(shè)計(jì)和選型來看,閥門的接管設(shè)計(jì)不合理,不宜采用承插焊接的結(jié)構(gòu),宜采用閥門整體制造凸臺(tái)后,與接管進(jìn)行對(duì)焊連接。
3、防范措施和建議
針對(duì)此次高壓雙閥聯(lián)體閥焊縫撕裂事故,對(duì)裝置的生產(chǎn)和管理提出以下建議和防范措施,以降低類似事故再次發(fā)生的概率,為生產(chǎn)裝置的長(zhǎng)期安穩(wěn)運(yùn)行提供有力保障。
(1)在設(shè)備采購、進(jìn)貨、驗(yàn)收、安裝、搶修、維修等各環(huán)節(jié)上都要把好關(guān),搞好質(zhì)量管理,確保質(zhì)量完好率;
(2)通過對(duì)設(shè)備、設(shè)施、裝置實(shí)際運(yùn)行及管理狀況的安全性進(jìn)行評(píng)價(jià),查找生產(chǎn)運(yùn)行中存在的危險(xiǎn)、有害因素,提出消除、預(yù)防或減弱其危害程度的技術(shù)措施和建議,為后續(xù)的安全生產(chǎn)提供依據(jù);
(3)提高日常生產(chǎn)巡檢質(zhì)量。加強(qiáng)監(jiān)督管理和檢查考核,增強(qiáng)員工認(rèn)真巡檢的自覺性,消除巡檢上的盲區(qū),尤其是不易引起注意的閥門、法蘭等部位,注意其完好性,及時(shí)發(fā)現(xiàn)事故苗頭,努力消除和控制,消除人的不安全行為,做到防患于未然。
(4)對(duì)關(guān)鍵部位的重點(diǎn)設(shè)備進(jìn)行定期預(yù)防性檢護(hù)維修,提高防范意識(shí),變事后處理為事先預(yù)防,真正貫徹實(shí)現(xiàn)“安全第一、預(yù)防為主”的安全生產(chǎn)方針。
(5)加強(qiáng)安全培訓(xùn)力度。強(qiáng)化對(duì)員工的安全技能培訓(xùn),提高員工對(duì)危險(xiǎn)物質(zhì)物化性質(zhì)及危險(xiǎn)性的認(rèn)識(shí),加強(qiáng)員工對(duì)所在裝置危險(xiǎn)情況的了解,落實(shí)臨氫環(huán)境、硫化氫環(huán)境作業(yè)的安全措施。加強(qiáng)對(duì)同類事故案例的剖析,從中吸取教訓(xùn),提高安全意識(shí)和安全技能。
4、結(jié)語
對(duì)新建蠟油加氫處理裝置,開工生產(chǎn)過程中發(fā)生的一起高壓雙閥聯(lián)體閥焊縫撕裂未遂事件進(jìn)行深層次的原因剖析,從而采取有效的措施和對(duì)策,能夠?yàn)檠b置的安穩(wěn)長(zhǎng)運(yùn)行,起到保駕護(hù)航的關(guān)鍵作用。