高壓大口徑全焊接閥體管線球閥國產化歷程
一、歷程
2000年之前,我國擁有2萬km長輸管線,只占全世界260萬km管線的0.8%。全焊接閥體管線球閥無一例外地采用美國Cameron公司產品。 2000年之后,在國家關于開發西部,使用綠色能源的政策指導下,起動西氣東輸一線工程,從新疆輪南至上海,全長4200km,管徑42″(1″=25.4mm,下同),輸送壓力10MPa。其中全焊接閥體緊急切斷閥全部采購國外產品,分體式鍛鋼閥體管線球閥則由上海耐萊斯·詹姆斯伯雷閥門有限公司供貨。與此同時,國家發改委提出《全焊接閥體管線球閥》國產化計劃。四川自貢高壓閥門股份有限公司取得國家財政支助,從意大利新比隆(NewoPignone)公司引進全套全焊接閥體管線球閥技術資料、工藝和裝備,2003年試制成功第一臺全焊接閥體管線球閥。上海耐萊斯·詹姆斯伯雷閥門有限公司在國家財政支助下,聯合高校,發揮地區優勢,自主開發研制全焊接閥體管線球閥,于2005年試制成功筒狀和球狀的閥體全焊接管線球閥,并擁有自主的知識產權,可以提供Class600,DN800(NPS32)以下管線球閥,且在澀寧蘭復線上服役。
2008年西氣東輸二線工程的起動,從新疆到上海再到廣州,全長8800km,選用管線直徑DN1200(NPS48),輸送壓力12MPa,這樣就需要Class900,DN1200(NPS48)全焊接閥體管線球閥。這種高壓大口徑全焊接管線球閥,2007年在全世界服役的僅13臺。二線工程的主干線上,40″Class600以上的緊急切斷閥亦全部從國外進口。32″以下在國內采購。同時,在國家能源局的主持下,2009年4月在沈陽召開“天然氣長輸管線關鍵設備國產化”工作會議,張國寶主任和中石油廖永遠副總經理參加會議,指示大口徑高壓全焊接管線球閥國產化,應予立項,這對降低西氣東輸工程造價,保證國家能源供應的安全,振興裝備制造業具有重要意義。并于2009年11月23日在北京釣魚臺國賓館召開天然氣長輸管道關鍵設備國產化啟動及簽約儀式。中石油與上海耐萊斯·詹姆斯伯雷閥門有限公司簽訂10臺Class600,Class900磅級,口徑DN1000,DN1200大口徑高壓全焊接閥體管線球閥的技術開發合同。在6個月的生產周期內完成了試制任務,并于2011年通過工業性運行試驗,產品已在西氣東輸三線服役。
十年磨一劍,我國已完成高壓大口徑全焊接閥體管線球閥的國產化工作,可以為國內外提供壓力等級從Class150,25001b級(11b=0.45kg),通徑從2″~60″球狀或筒狀全焊接閥體或分體式閥體的管線球閥。圖1為上海耐萊斯·詹姆斯伯雷閥門有限公司生產的Class900,48″高壓大口徑全焊接閥體管線球閥。并與2012年4月承接西氣東輸三線Class900,48″全焊接閥體管線球閥32臺,2012年年底完工正式交付使用。
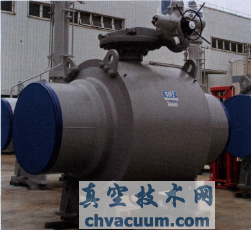
圖1 Class 900.48''高壓大口徑全焊接閥體管線球閥
二、創新
和管道工業一樣,2000年我國全焊接閥體管線球閥落后于國外近半個世紀。然而,我國開發這一全焊接產品是在21世紀,可以充分運用現代化設計技術與現代制造技術,起步晚但起點高。整個開發過程一方面應用反求工程,消化吸收國外各個閥門公司之所長,綜合為我所用;另一方面運用現代數值分析方法來解決產品設計和焊接工藝上的技術問題,運用現代斷裂學理論解決大厚度窄間隙埋弧焊焊縫免焊后熱處理的技術難點。因此,在研制開發過程中,有很多方面擁有自行的知識產權,取得國際領先地位。
1.閥體強度的應力分析
早于2004年,采用ASMEⅧ鍋爐壓力容器第二分冊分析法,通過有限元分析,計算在外載荷與內壓復合作用下閥體的應力強度。提出筒式閥體在閥頸處存在應力集中,建議采用焊接閥頸結構。這一分析和建議已被國內外主要閥門公司認可和采用。
2.低殘余應力焊接工藝參數的優化
全焊接閥體管線球閥的關鍵技術是焊接,其難點是焊接最后一道工序不能進行熱處理。因此,對焊接過程的溫度場、應力場和焊接變形進行預測和控制,上海耐萊斯·詹姆斯伯雷閥門有限公司與上海交通大學合作,首先用數值分析方法對焊接過程溫度場,應力場進行預測和控制,采用“固有應變法”對閥體焊接變形進行預測和控制(見圖2),并與實際測定的溫度場,殘余應力和變形值相比較,從而優化焊接工藝參數在較低的殘余應力水平上,為焊后免熱處理提供條件。
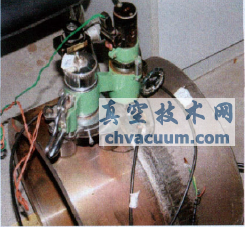
圖2 應力場的測定
3.焊縫免焊后熱處理(PWHT)的安全評估
根據API6D與ASME標準的相關規定,大于38mm以上厚度的焊縫必須進行熱處理,而產品中有橡膠彈性體,不能進行熱處理,國外的閥門公司無一對此做出科學的解析和安全評估。國內首先應用斷裂學理論,按照英國BS7448第二部分《斷裂韌性試驗》的方法,采用美國API1104附錄A《管道焊接與相關設施》的評定與驗收標準,對全焊接閥體焊縫試樣做全厚度斷裂性CTOD試驗以及殘余應力測定,根據結果做出免焊后熱處理的安全評估。圖3為在液壓萬能試驗機上,CTOD試驗過程,試驗溫度-46℃,二次加載直至試驗失穩。
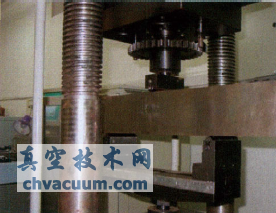
圖3 CTOD試驗預制疲勞裂紋試驗過程
4.過渡段材料的優化
運用篩選工程,對國外閥門公司采用A694《高壓傳送設施法蘭管件、閥門材料和零件用鍛造碳鋼和合金鋼材料》標準中的F60、F52作為過渡段材料提出質疑。這一標準既不是閥門標準B16.34的引用標準,又不是管道標準B31.8的引用標準,沒有標準支持,是選用錯誤。這一結論已被美國工程師協會ASMEB16.34專業委員會和美國試驗和材料協會ASTMA694專業委員會的答復中被確認,從而使我國長輸管線工程的安全性得到進一步保證。
三、崛起
高壓大口徑全焊接管線球閥的國產化過程,亦是傳統制造業改造成現代先進閥門制造業的過程,現代先進制造業是一個技術經濟群體,是指將原材料和其他生產要素,經濟地、合理地轉化為高附加值、高技術產品的一個基地。擁有現代設計技術,現代先進制造裝備和制造工藝以及系統化的現代化管理技術。在高壓大口徑全焊接閥體管線球閥的國產化過程中,上海耐萊斯·詹姆斯伯雷閥門有限公司充分運用現代設計技術,如應用反求工程技術,解決閥體材料的化學成分和機械性能;運用篩選工程技術提出用A350LF6材料替代國外傳統的A694F60材料作為閥體過渡段用材;運用數值分析方法,指出傳統閥體設計中應力集中,采用焊接閥頸優化閥體結構設計;運用數值分析方法,精確地預測閥體的焊接變形,優化焊接殘余應力的焊接工藝參數;運用彈塑性斷裂力原理論解決焊縫免焊后熱處理的安全評估和驗收標準;運用數值分析法對閥體在外載荷和內壓復合作用下的應力強調分析和抗震計算。
在裝備上,擁有從意大利進口的車磨一體化的大型球體數控車球磨磨球機(見圖4),擁有大型數控立車和大型臥式鏜銑加工中心,以及全國首臺3200t液壓試驗設備、自動埋弧焊機(見圖5)、美國進口三坐標測試儀,大扭矩測試傳感器及火燒試驗等現代化先進的閥門制造裝備和試驗設備。

圖4 大型球體數控車球磨磨球機
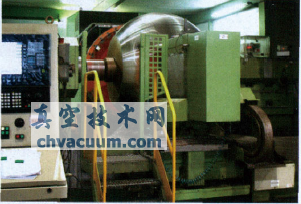
圖5 自動埋弧焊機
上海耐萊斯·詹姆斯伯雷閥門有限公司在國家發改委和能源局的直接領導下,取得高壓大口徑全焊接閥體管線球閥批量生產成功,并在通過工業性試驗的基礎上,上海電氣集團將投資擴建7000m2大口徑管線球閥的裝配、焊接、試驗生產線,添置超大型4500t液壓試驗設備和3.15m大型數控立車,形成年產40″~60″管線球閥150臺,36″以下管線球閥1500臺的能力,建成一個現代化先進的閥門制造企業,為我國管道工業作出貢獻。