超臨界汽輪機單順閥切換問題的一些探討
一、引言
我廠汽輪機是由是哈爾濱汽輪機廠自主開發(fā)的、具有自主知識產(chǎn)權(quán)的超臨界、一次中間再熱、單軸、三缸、四排汽、直接空冷凝汽式660MW汽輪機組,采用積木式的設計,保留了濕冷機組的技術(shù)特點如反動式葉片、整鍛轉(zhuǎn)子、多層汽缸、數(shù)字電液調(diào)節(jié)等。其結(jié)構(gòu)緊湊,經(jīng)濟性好,適合中國國情,具有很高的運行效率和安全可靠性。
二、單閥/順序閥(SIN/SEQ)
單閥/順序閥切換的目的是為了提高機組的經(jīng)濟性和快速性,實質(zhì)是通過噴嘴的節(jié)流配汽(單閥控制)和噴嘴配汽(順序閥控制)的無擾切換,解決變負荷過程中均勻加熱與部分負荷經(jīng)濟性的矛盾。單閥方式下,蒸汽通過高壓調(diào)節(jié)閥和噴嘴室,在360°全周進入調(diào)節(jié)級動葉,調(diào)節(jié)級葉片加熱均勻,有效地改善了調(diào)節(jié)級葉片的應力分配,使機組可以較快改變負荷;但由于所有調(diào)節(jié)閥均部分開啟,節(jié)流損失較大。順序閥方式則是讓調(diào)節(jié)閥按照預先設定的次序逐個開啟和關閉,在一個調(diào)節(jié)閥完全開啟之前,另外的調(diào)節(jié)閥保持關閉狀態(tài),蒸汽以部分進汽的形式通過調(diào)節(jié)閥和噴嘴室,節(jié)流損失大大減小,機組運行的熱經(jīng)濟性得以明顯改善,但同時對葉片存在產(chǎn)生沖擊,容易形成部分應力區(qū),機組負荷改變速度受到限制。因此,冷態(tài)啟動或低參數(shù)下變負荷運行期間,采用單閥方式能夠加快機組的熱膨脹,減小熱應力,延長機組壽命;額定參數(shù)下變負荷運行時,機組的熱經(jīng)濟性是電廠運行水平的考核目標,采用順序閥方式能有效地減小節(jié)流損失,提高汽機熱效率。
對于定壓運行帶基本負荷的工況,調(diào)節(jié)閥接近全開狀態(tài),這時節(jié)流調(diào)節(jié)和噴嘴調(diào)節(jié)的差別很小,單閥/順序閥切換的意義不大。對于滑壓運行調(diào)峰的變負荷工況,部分負荷對應于部分壓力,調(diào)節(jié)閥也近似于全開狀態(tài),這時閥門切換的意義也不大。對于定壓運行變負荷工況,在變負荷過程中希望用節(jié)流調(diào)節(jié)改善均熱過程,而當均熱完成后,又希望用噴嘴調(diào)節(jié)來改善機組效率,因此這種工況下要求運行方式采用單閥/順序閥切換來實現(xiàn)兩種調(diào)節(jié)方式的無擾切換。以求得最好的運行工況。
我廠#1、#2機組投產(chǎn)以來,運行方式一直采用全周進汽的單閥運行方式,這樣轉(zhuǎn)子和定子的溫差較小,在變負荷運行時溫差影響較小,有利于機組初期的磨合。由于單閥運行,4個高壓調(diào)節(jié)閥(GV)都參與開度調(diào)節(jié),且一般高壓調(diào)門開度不大(20%-50%),蒸汽通過調(diào)節(jié)閥門時有較大的節(jié)流損失,而機組運行要求盡量減少調(diào)節(jié)閥門的節(jié)流損失,提高汽輪機的效率,提高經(jīng)濟性。而且閥門的節(jié)流損失在閥門接近全關或接近最大流量時達到最小。采用順序閥門控制方式下,一般只有一個高壓調(diào)節(jié)閥進行開度調(diào)節(jié),其余的閥門保持全開或全關,這樣減少了節(jié)流損失,提高機組熱效率。
哈汽大部分現(xiàn)役機組其順序閥設計次序基本全部為:GV1/GV2→GV3→GV4;關閉順序閥的次序:GV4→GV3→GV1/GV2。汽機控制汽門示意圖如下:
三、出現(xiàn)的問題及分析
我廠1號機組單順閥切換過程中,從DCS監(jiān)控畫面取得的機組轉(zhuǎn)速、負荷、1瓦x向、y向振動數(shù)值曲線分析,單閥切至順閥運行后,1瓦軸振明顯增大,增大幅度達40~50μm,同時伴隨著1、2瓦回油溫度上升約5~10度之間。比對分析,造成這些問題的原因以及國內(nèi)其它機組普遍出現(xiàn)的問題有以下三點,并有針對性的理論結(jié)合試驗提出解決方案。
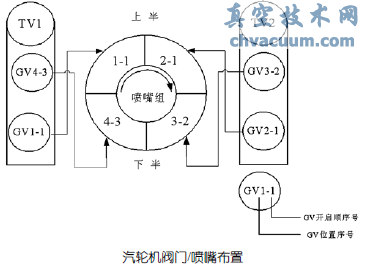
1、采用順閥運行噴嘴配汽時,調(diào)節(jié)級分為若干個噴嘴組,它們處于非對稱性的部分進汽狀態(tài)。汽流力合力不能相互完全抵消,及蒸汽除了在轉(zhuǎn)子調(diào)節(jié)級葉輪上產(chǎn)生力矩而使轉(zhuǎn)子旋轉(zhuǎn)外,還有一個通過轉(zhuǎn)子中心的合力,進汽的不平衡造成壓力徑向分布不均和轉(zhuǎn)子轉(zhuǎn)矩徑向不平衡,軸承的穩(wěn)定性降低及轉(zhuǎn)子在汽缸中的位置不對中,因此,存在配汽剩余汽流力,這是產(chǎn)生汽流激振的根本原因。根據(jù)上述對力的分析,轉(zhuǎn)子將受到不同方向的蒸汽激振和切向分力的影響,引起軸承受力變化,使軸系中各軸承載荷及轉(zhuǎn)子撓度發(fā)生變化,嚴重時將使轉(zhuǎn)子軸系產(chǎn)生不穩(wěn)定運行,使轉(zhuǎn)子失穩(wěn)引起較大的振動,調(diào)門的動作又會使調(diào)節(jié)級的配汽剩余汽流力發(fā)生變化,往往會因軸系、通流結(jié)構(gòu)設計及配汽特性調(diào)整不良等原因,使運行存在如軸瓦溫度高、軸振不穩(wěn)定、低頻渦動、汽流激振動等一系列問題,影響機組的安全穩(wěn)定運行,實際運行也證實了這一系列問題的存在。
對此,消除配汽剩余汽流力便是解決問題的關鍵。從理論上分析力的矢量和以及對國內(nèi)同類型機組的調(diào)查,我們提出解決方案:更改順序閥開啟順序,將原GV1/GV2→GV3→GV4變?yōu)镚V1/GV3→GV2→GV4。
2、汽輪機在順閥運行時,先后開啟的高壓調(diào)門之間存在明顯的重疊度,重疊度最小時為零,此時它的調(diào)節(jié)級效率最高,但流量特性最差,會引起機組在某些負荷不穩(wěn)定。重疊度最大的曲線流量特性的線性度最好,但調(diào)節(jié)級效率最低。在順序閥開啟時,可能會存在某段流量范圍內(nèi)流量指令與實際蒸汽流量不成線性,這時需要開啟下一個調(diào)門來修正,這就是閥門重疊度的設置。如下圖所示:
實線所示為無重合度的情況,這不負荷調(diào)節(jié)系統(tǒng)的設計要求(調(diào)節(jié)系統(tǒng)的靜態(tài)特性線要求兩端速度變動率大,中間平滑過渡),虛線所示為合理重合度的情況。
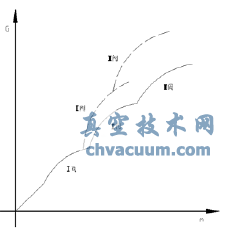
為了使配汽機構(gòu)特性曲線比較平滑,一般在前閥尚未開完,其閥門壓力重疊度為0.85~0.9時便提前開啟后閥。調(diào)門重疊度的大小直接影響著配汽機構(gòu)的靜態(tài)特性。重疊度有兩種:
1、行程重疊度

2、壓力重疊度

一般情況下,當汽門開度達到60%時,汽門的通流能力達到總通流能力的90%以上,在“閥點”附近,先開啟的調(diào)節(jié)汽門不可避免的存在40%左右的空行程,此時,高壓調(diào)節(jié)閥極可能頻繁出現(xiàn)大幅度晃動,嚴重影響機組的安全運行。
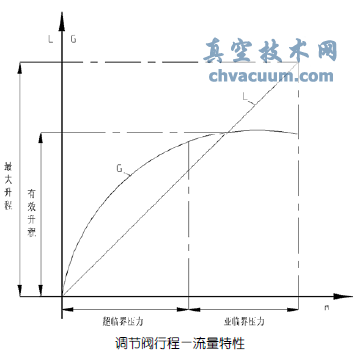
試驗處理辦法:順閥運行方式下,進行負荷變動試驗,升負荷、降負荷兩個階段,試驗是機組協(xié)調(diào)控制投入,主蒸汽壓力按滑壓曲線確定,按正常變負荷速度,連續(xù)同向改變負荷,判斷“閥點”處閥門的晃動情況,如果存在明顯晃動,要對配汽特性曲線進行調(diào)整,通過修改配汽特性曲線找到機組運行的最佳配汽工況點,從根本上解決改問題。
2、配汽特性流量曲線改變,理想的配汽特性曲線在不同的配汽方式下表現(xiàn)出來的各個高壓調(diào)節(jié)汽門雖然開度不同,但通過的總蒸汽流量是相同的,而在實際應用中,由于種種原因,切換前后總蒸汽流量將產(chǎn)生偏差,這種偏差直接反映到機組功率與主蒸汽參數(shù)的變化上。下圖是通過運行過程中,機組行程、閥后流量實際測量值的單閥、順閥的流量特性曲線圖。
通過上圖我們可以看出單、順閥流量特性曲線的差別,以及各個高壓調(diào)節(jié)閥的“閥點”在圖中所對應的位置,并據(jù)此,在運行當中密切觀察“閥點”處調(diào)閥晃動和機組振動、瓦溫等情況,對曲線進行修正,以達到最佳流量曲線。
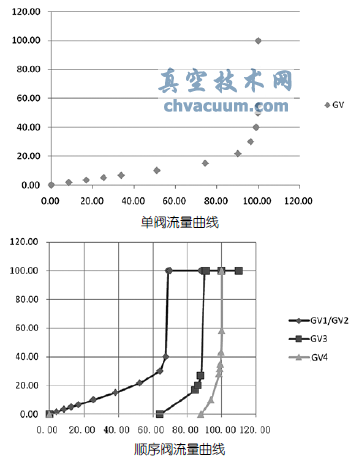
四、結(jié)論
將原順序閥次序:GV1/GV2→GV3→GV4,改變?yōu)椋篏V1/GV3→GV2→GV4,對稱進汽,消除配汽剩余汽流力,避免產(chǎn)生汽流激振,對機組滑壓運行兩種配汽模式的比較分析。試驗設計單閥模式運行,維持負荷在額定之50%即300MW左右穩(wěn)定運-~5-o.5h以上。全面記錄汽輪機運行各參數(shù),如主、再熱蒸汽溫度、壓力、軸向位移、高壓缸脹差、汽缸溫度、調(diào)節(jié)級壓力等,在單閥模式滑參數(shù)將機組負荷逐漸升至額定600MW,主蒸汽滑壓范圍11.40MPa~16.59MPa,溫度保持533~C不變。過程中每50MW停留0.5h,全面記錄運行各參數(shù),期間回熱系統(tǒng)全部投入、輔機系統(tǒng)及附屬設備、汽機凝汽器終參數(shù)、軸承潤滑狀況等維持不變。在順序閥方式下,按同樣的主蒸汽滑參數(shù)曲線、運行方式進行比較試驗,以得出適應該機組的流量特性曲線,并保證運行中不偏離該曲線,達到安全運行的需要。