鉻鎳鋼齒輪滲碳淬火新工藝
鉻鎳鋼齒輪,特別是20Cr2Ni4鋼齒輪,以往由于滲碳淬火后表層存在大量的殘余奧氏體,所以在滲碳后淬火之前進行一次高溫回火,即一次淬火法。其生產率低,耗能多。經我們多年實踐,采用微機控制滲碳,實現齒輪滲碳后直接淬火工藝。
1、前言
我廠磨煤機減速箱齒輪有螺旋傘齒輪、圓柱齒輪,其外形尺寸最大直徑982mm,最大模數m=14,采用S17Cr2Ni2Mo,20Cr2Ni2Mo,J20CrNi2Mo鉻鎳滲碳鋼制造。也曾制造一批20Cr2Ni4鋼重載齒輪。其工藝路線:鍛造——正火加回火——粗車——消除應力——半精加工——滲碳淬火加低溫回火——精加工。
對齒輪的滲碳淬火,我們最初采用一次淬火法,即齒輪滲碳后進行高溫回火再加熱到淬火溫度進行淬火。由于我們只有一臺滴控井式滲碳爐,齒輪的滲碳、淬火、高溫回火都在這個爐子進行。生產周期長,不能滿足日益增長的生產量的需求,迫切需要改變現有的一次淬火法,實現齒輪滲碳后降至淬火溫度保溫30分鐘后進行油冷的直接淬火法。
經我們多次工藝試驗實現了這一目標。從1995年開始,每年要處理大小齒輪近百套,每爐節約20小時,每爐可節約1500kW·h(度),極大的提高了勞動生產率,滿足了生產的需要,如期完成總廠下達的生產任務。
2、合金滲碳鋼齒輪技術要求
為滿足使用要求,合金滲碳鋼齒輪技術要求:
1)齒輪鍛坯正火后的硬度HB≤229。
2)滲碳淬火后硬度:齒面58~62HRC,芯部40~45HRC。
3)齒面滲碳層深度:根據不同模數的齒輪,一般為1.5~2.5mm。
4)齒輪鍛坯奧氏體晶粒度6級以上,帶狀鐵素體在2級以下。
5)齒面滲碳淬火后組織為隱晶或細針狀馬氏體組織,不許有針狀和網狀碳化物及大量殘余奧氏體存在。碳化物3級以下合格,馬氏體加殘余奧氏體3級以下合格。心部淬火后為低碳馬氏體組織,心部鐵素體不允許超過2級。
6)齒面滲碳淬火后硬度梯度平緩,碳濃度平緩。
7)齒輪精度等級6級。
3、嚴格控制齒輪鍛坯的質量
我廠生產的減速箱齒輪鍛坯委托外廠冶煉鍛造。為確保鍛坯質量,對進廠的鍛坯都要進行復驗,其中包括表面質量,機械性能,非金屬夾雜物,低倍組織,奧氏體晶粒度,帶狀組織等必須達到技術要求的合格范圍。并用同一熔煉爐號,同一材料,同一鍛造工藝的鍛坯,制成與齒輪同模數的齒形(單齒)滲碳淬火試塊。
4、認真做好預備熱處理
齒輪鍛坯的預備熱處理的好壞直接關系到后序的滲碳淬火的質量。其中包括馬氏體針的粗細。嚴格執行正火加回火工藝,我們選用的正火溫度高于滲碳溫度20℃,即940℃保溫3小時空冷,650~700℃保溫4小時空冷。1OOKW臺車爐裝爐量8件,嚴格檢查齒輪鍛坯正火后的硬度和金相組織和晶粒度的檢查。組織為細珠光體,晶粒度優于6級。
5、齒輪滲碳淬火設備及工藝
我們使用150KW滴注式井式滲碳爐對齒輪進行滲碳淬火,其有效尺寸為Φ1200×1200,該爐靠爐蓋本身自重(約1噸重)及石棉盤根與爐罐密封,省去爐蓋和爐罐用螺栓、螺母連續的繁重體力勞動。經過冷熱調試,爐溫均勻,設備密封性能好,不漏氣。爐罐內爐氣碳勢均勻,波動小,920℃鋼箔定碳。當氧電勢E=1140mV時,爐罐內上下部位碳勢相差0.02%C;當氧電勢E=1125mV時,爐罐內上下部位碳勢相差0.03%C。
我們用熱電偶做爐溫的傳感元件,用氧探頭做氧電勢(爐氣碳勢)的傳感元件。用電磁閥和可控硅做碳勢和溫度的執行機構。滲碳介質采用工業甲醇加燈用煤油。使用時直接滴入氣體滲碳爐內,經裂解后產生活性碳原子,通過調節滴入量控制齒輪表面的碳濃度。我們采用了農機院工藝所研制的TC-890井式爐滲碳微機控制系統,內有滴注式可控氣氛滲碳、淬火過程控制程序。
滲碳工藝采用改進的強滲—擴散兩段工藝。兩段法具有滲碳速度快,滲層碳濃度控制質量好的優點。在此基礎上作了進一步改進。充分發揮計算機快速計算的控制功能,根據工況適時調節電磁閥的開啟頻率和脈沖寬度,調整甲醇、煤油量,并保持兩者之間的比例關系。從而逐步調節爐氣碳勢,使滲碳速度更快,齒面碳濃度平緩,淬火后齒面硬度梯度平緩,滲碳質量更好,稱之自適應滲碳法。
實踐證明,應用微機控制系統,工人操作簡單,工人只要輸入鋼材代號,要求的硬化層深度和表面含碳量,其一切都由電腦自動控制完成,當硬化層深度和表面含碳量達到預定的目標值時,自動鳴鈴提示操作人員出爐。在整個滲碳過程中各工藝參數用數碼管顯示,并能打印記錄。通過對齒表面碳含量的測定,與表面碳濃度設定值0.70%C比較,該控制系統能使輪齒表面碳濃度精確控制在±0.05%C。齒輪表面碳濃度、淬火溫度的高低直接關系到齒輪淬火后馬氏體針的粗細和殘余奧氏體量的多少。當齒面碳濃度及淬火溫度過高時,在淬火加熱時溶入奧氏體中的碳含量就會增加,降低了馬氏體的轉變,使鋼中的殘余奧氏體增多。淬火溫度過低使輪齒芯部硬度低,降低輪齒心部的機械性能。經多爐試驗確定如下滲碳淬火工藝。我們把輪齒表面碳濃度控制在0.70%C,滲碳溫度920℃。滲碳結束后降至淬火溫度為840℃,保溫30分鐘油冷。淬火油采用北京華立精細化工公司的快速淬火油,保證了組織充分轉變。
6、齒輪回火設備及工藝
我們使用100KW井式回火爐,有效尺寸Φ1200×1200,使用培特永昌機電有限責任公司生產的微機控制系統,經用6支凱裝熱電偶在爐罐上、中、下部各點測量爐溫的均勻性。當儀表指示為180℃時,最大溫差為5℃。
齒輪滲碳淬火后,必須及時回火。回火的目的是為降低淬火應力,減少脆性,盡量保持鋼的高硬度和高耐磨性。使齒面硬度保持在58~62HRC。
馬氏體分解速度同回火溫度、回火時間有密切關系。回火溫度愈高,馬氏體分解速度愈快,析出的c碳化物愈多,因而馬氏體的碳濃度和正方度也愈低。因此,必須找出—個適當的回火溫度,既保證齒面的高硬度,又使馬氏體充分分解,降低馬氏體的過飽和度。回火需保溫—定時間,目的是使工件表面與心部溫度均勻一致,保證組織轉變的充分進行。經過試驗做出輪齒表面硬度和回火溫度的關系曲線圖(見圖1)
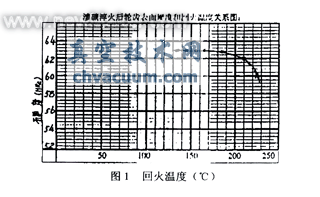
我們采用180℃保溫6小時空冷的兩次回火工藝。
滲碳淬火齒輪經過回火后檢查齒面硬度都能保證58~62HRC,齒面碳化物控制在1~3級,馬氏體加殘余奧氏體控制在1~3級(見圖2)。心部鐵素體控制在1級。
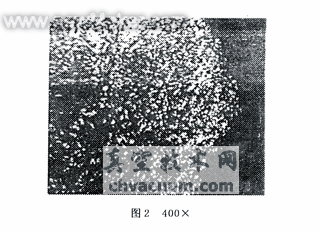
7、結論
鉻鎳鋼齒輪滲碳淬火,只要嚴格控制齒輪鍛坯的內在質量,奧氏體晶粒度優于等于6級。認真執行正火加回火工藝,做好滲碳淬火前的組織準備。使用先進的淬火、回火設備,采用微機控制系統,精確控制齒面的碳濃度,淬火、回火溫度,就可以實現直接淬火工藝。
從1995年至今,我們一直使用鉻鎳鋼齒輪滲碳淬火工藝,從未發生任何質量問題。l995年制造的ZG’M95磨螺傘齒輪至今仍在使用中。